Clamp for battery laser welding
A battery laser welding, laser welding machine technology, applied in the direction of laser welding equipment, welding equipment, welding equipment, etc., can solve the problems of weak welding, affecting production efficiency, left and right shaking, etc., to prevent the welding from being weak and easy to fall off, The effect of improving welding quality and structural stability
- Summary
- Abstract
- Description
- Claims
- Application Information
AI Technical Summary
Problems solved by technology
Method used
Image
Examples
Embodiment Construction
[0027] The preferred embodiments of the present invention will be described below in conjunction with the accompanying drawings.
[0028] Such as Figure 1 to Figure 4 and Figure 7As shown, the present invention provides a jig for battery laser welding, including a positioning jig 1 and a jig body 2 fixed on a laser welding machine. The upper end surface of the positioning jig 1 is recessedly formed with at least one positioning groove 10 for accommodating the electric core, one end of the positioning groove 10 is open, and the positioning jig 1 is also provided with a side and accommodate the slot 11 of the PCM board. The clamp body 2 includes a positioning seat 20 , a linear drive device 21 , a mounting plate 221 , a fixing plate 23 and at least two pressing and positioning components 24 . The positioning seat 20, the linear drive device 21 and the mounting plate 221 are fixed to the laser welding machine, the mounting plate 221 stands upward, and the upper end surface o...
PUM
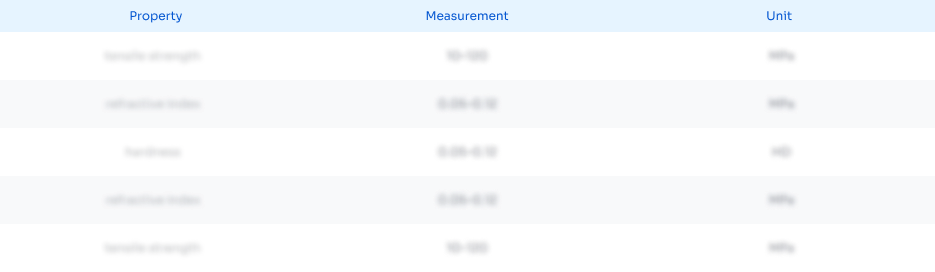
Abstract
Description
Claims
Application Information

- R&D
- Intellectual Property
- Life Sciences
- Materials
- Tech Scout
- Unparalleled Data Quality
- Higher Quality Content
- 60% Fewer Hallucinations
Browse by: Latest US Patents, China's latest patents, Technical Efficacy Thesaurus, Application Domain, Technology Topic, Popular Technical Reports.
© 2025 PatSnap. All rights reserved.Legal|Privacy policy|Modern Slavery Act Transparency Statement|Sitemap|About US| Contact US: help@patsnap.com