A method for extracting zinc oxide from ironmaking blast furnace dust
An iron-smelting blast furnace, zinc oxide technology, applied in the direction of zinc oxide/zinc hydroxide, etc., can solve the problems of high energy consumption, high temperature, furnace blockage, etc., and achieve long operation cycle, convenient reuse, low iron content in tailings Effect
- Summary
- Abstract
- Description
- Claims
- Application Information
AI Technical Summary
Problems solved by technology
Method used
Image
Examples
Embodiment Construction
[0016] The present invention utilizes vertical airtight furnace equipment for production, and the structure of the airtight furnace equipment is as attached figure 2 shown. The dedusting and ash ball pressing machine 1 is connected to the top charging port 3-1 of the closed furnace 3 through the elevator 2. The middle part of the closed furnace 3 is a high temperature zone 3-2, and the lower part of the high temperature zone 3-2 is the air inlet zone 3-3. The bottom of the closed furnace 3 is the solid tailings discharge area 3-4. One side of the upper part of the closed furnace 3 is connected to the upper part of the reaction furnace 4 through a pipeline, and the lower part of the reaction furnace 4 is connected to the recovery device 6 and the purification device 7 in sequence through the pipeline, and the purification device 7 is connected. To the finished product tank 8, the bottom of the recovery device 6 and the purification device 7 is provided with a dust collector 9....
PUM
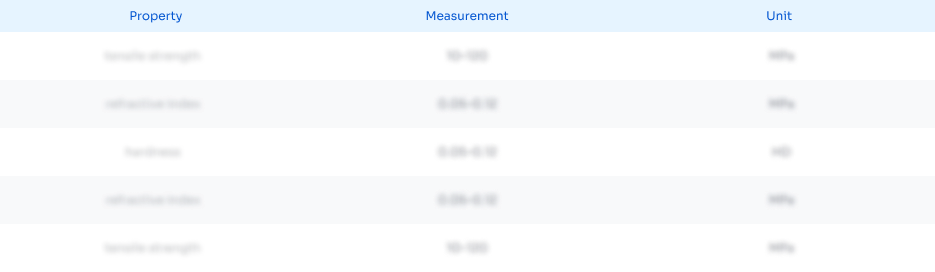
Abstract
Description
Claims
Application Information

- R&D
- Intellectual Property
- Life Sciences
- Materials
- Tech Scout
- Unparalleled Data Quality
- Higher Quality Content
- 60% Fewer Hallucinations
Browse by: Latest US Patents, China's latest patents, Technical Efficacy Thesaurus, Application Domain, Technology Topic, Popular Technical Reports.
© 2025 PatSnap. All rights reserved.Legal|Privacy policy|Modern Slavery Act Transparency Statement|Sitemap|About US| Contact US: help@patsnap.com