Method for prefabricating camber of large-scale steel laminated beam web
A beam web and camber technology, applied in the field of large-scale steel stacked beam manufacturing, can solve the problems of inability to correct, large amount of correction, huge structure, etc., achieve high practical value, and ensure the effect of flatness
- Summary
- Abstract
- Description
- Claims
- Application Information
AI Technical Summary
Problems solved by technology
Method used
Image
Examples
Embodiment Construction
[0020] Attached below Figure 1-7 An embodiment of the present invention is described.
[0021] A method for prefabricating the web camber of a large-scale steel stacked beam includes the following steps:
[0022] 1. First, the upper beam web 2 and the lower beam web 5 are blanked on the sides of the upper beam flange plate 1 and the lower beam flange plate 4 respectively according to the ideal curve of the prefabricated camber, and the upper beam web 2 and the lower beam web are 5. The upper beam laminated slab 3 and the lower beam laminated slab 6 sides are cut according to a straight line without prefabricating the camber; specifically, a semi-automatic cutting machine is used to cut and blank the material with a combination of shorter fold lines instead of arc curves. Make the camber of the upper beam web 2 be f1, and the camber of the lower beam web 5 be f2;
[0023] 2. Using the principle of flame rectification, the upper beam web 2 and the lower beam web 5 are band-sh...
PUM
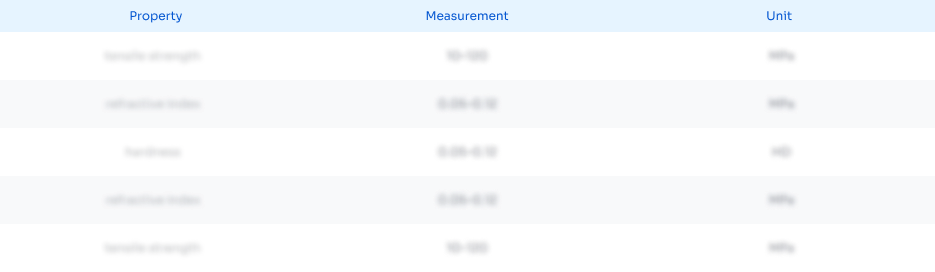
Abstract
Description
Claims
Application Information

- Generate Ideas
- Intellectual Property
- Life Sciences
- Materials
- Tech Scout
- Unparalleled Data Quality
- Higher Quality Content
- 60% Fewer Hallucinations
Browse by: Latest US Patents, China's latest patents, Technical Efficacy Thesaurus, Application Domain, Technology Topic, Popular Technical Reports.
© 2025 PatSnap. All rights reserved.Legal|Privacy policy|Modern Slavery Act Transparency Statement|Sitemap|About US| Contact US: help@patsnap.com