Wafer level packaging method for LED (Light-Emitting Diode) chip level white light source
A LED chip and wafer-level packaging technology, applied in semiconductor devices, electrical components, circuits, etc., can solve problems such as low yield, affecting LED yield, uneven color of LED product space, etc., to promote development and innovation, The effect of improving LED packaging efficiency and good overall color temperature consistency
- Summary
- Abstract
- Description
- Claims
- Application Information
AI Technical Summary
Problems solved by technology
Method used
Image
Examples
Embodiment 1
[0038] see Figure 1(a) and 1(b) , the LED flip chip 11 is integrated on the LED packaging wafer substrate 13 suitable for flip chip packaging through the solder layer 12 and the crystal bonding process, so as to realize the electrical connection and mechanical fixation of the flip chip electrode 19 and the substrate electrode 14 . Referring to Fig. 1(c), through the extrusion molding method with the surface roughening mold 15 containing the phosphor powder layer containing the phosphor powder glue 16, the LED wafer integrated with the LED flip chip is cured at a high temperature of 120°C to form a uniform Phosphor powder layer 17 with a thickness of 1.5 g / ml in the phosphor material used in the phosphor powder glue, and the thickness of the formed phosphor powder layer is 250 microns. Subsequently, the surface roughening mold 15 containing the phosphor layer is separated from the phosphor layer 17, and the encapsulation effect achieved is that a phosphor layer with a uniform...
Embodiment 2
[0040] see Figure 2(a) and 2(b), the LED flip chip 11 is integrated on the LED packaging wafer substrate 13 suitable for flip chip packaging through the solder layer 12 and the crystal bonding process, so as to realize the electrical connection and mechanical fixation of the flip chip electrode 19 and the substrate electrode 14 . Referring to Fig. 2 (c), through the extrusion molding method of the phosphor layer mold 21 containing the phosphor powder glue 16 and the phosphor layer with the phosphor layer prepared on the LED wafer integrated with the LED flip chip, through 120 The phosphor layer 22 with a convex structure is formed at a high temperature of ℃, and the concentration of the phosphor material in the phosphor glue used is 1.0 g / ml, and the thickness of the formed phosphor layer is 200 microns, and the height of the protrusion is 120 Microns. Subsequently, the surface roughening mold 15 containing the phosphor layer is separated from the phosphor layer 22 contain...
Embodiment 3
[0042] see Figure 3(a) and 3(b) , the LED flip chip 11 is integrated on the LED packaging wafer substrate 13 suitable for flip chip packaging through the solder layer 12 and the crystal bonding process, so as to realize the electrical connection and mechanical fixation of the flip chip electrode 19 and the substrate electrode 14 . Referring to FIG. 3( c ), the semi-cured phosphor layer film 31 used for wafer-level packaging is applied on the wafer by a vacuum embossing method to achieve a phosphor layer coating with a uniform thickness. Then the semi-cured phosphor layer film is cured at 120° C., wherein the concentration of the phosphor material in the phosphor layer film used is 2.0 g / ml, and the thickness of the formed phosphor layer is 150 microns. Then the support film 32 on the phosphor layer film 31 is peeled off by a robot. The encapsulation effect achieved is that a phosphor layer with a uniform thickness is coated on the wafer as shown in FIG. 3( d ). In order t...
PUM
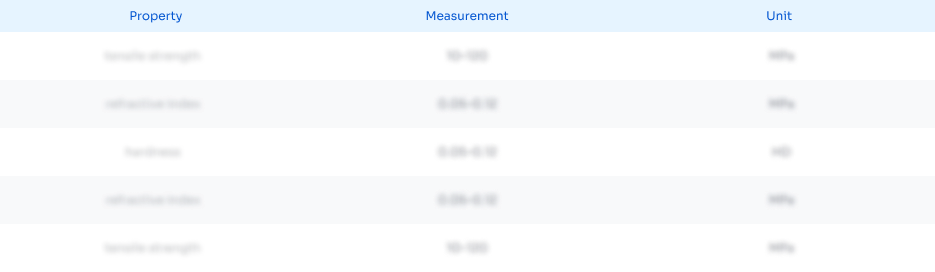
Abstract
Description
Claims
Application Information

- Generate Ideas
- Intellectual Property
- Life Sciences
- Materials
- Tech Scout
- Unparalleled Data Quality
- Higher Quality Content
- 60% Fewer Hallucinations
Browse by: Latest US Patents, China's latest patents, Technical Efficacy Thesaurus, Application Domain, Technology Topic, Popular Technical Reports.
© 2025 PatSnap. All rights reserved.Legal|Privacy policy|Modern Slavery Act Transparency Statement|Sitemap|About US| Contact US: help@patsnap.com