Clamp for metal thin-wall whole segment tube axial tension and compression fatigue test
A fatigue test, metal thin technology, applied in the field of fatigue test, can solve the problems of lock nut stress concentration, reduce the service life of the fixture, fixture damage and other problems, achieve the effect of reducing stress concentration, prolonging the service life and improving the clamping force
- Summary
- Abstract
- Description
- Claims
- Application Information
AI Technical Summary
Problems solved by technology
Method used
Image
Examples
Embodiment Construction
[0026] The present invention will be further described below in conjunction with the accompanying drawings.
[0027] A jig for axial tension-compression fatigue test of metal thin-walled full-section pipes; including a fixed frame 1, a core sleeve 2, a mandrel 3, an outer jacket 4, bolts 5, and lock nuts 6;
[0028] Core sleeve 2—The upper end of core sleeve 2 is a T-shaped double shoulder with internal thread, and the lower end is a symmetrical four-petal inner cone sleeve. The inner sleeve part of the upper shoulder of core sleeve 2 is internal thread, and the lower end of core sleeve 2 The inner side is a smooth inner cone structure, the outer side of the shoulder at the upper end of the core sleeve 2 is an external thread, and the lower end is a smooth outer wall;
[0029] Mandrel 3—The upper end of the mandrel 3 is a hexagonal nut, the middle end is a screw with external threads, and the lower end is a smooth outer cone shape; the size of the middle end screw of the mandr...
PUM
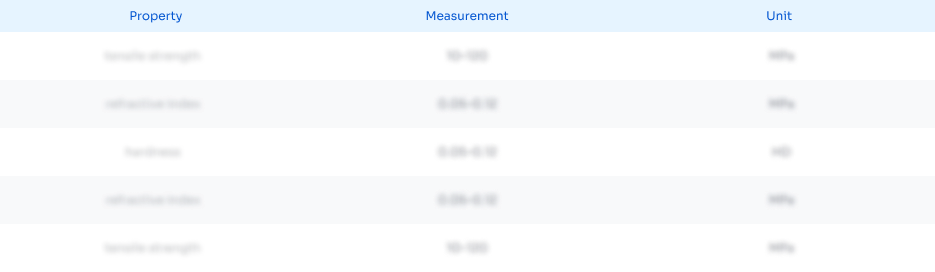
Abstract
Description
Claims
Application Information

- R&D
- Intellectual Property
- Life Sciences
- Materials
- Tech Scout
- Unparalleled Data Quality
- Higher Quality Content
- 60% Fewer Hallucinations
Browse by: Latest US Patents, China's latest patents, Technical Efficacy Thesaurus, Application Domain, Technology Topic, Popular Technical Reports.
© 2025 PatSnap. All rights reserved.Legal|Privacy policy|Modern Slavery Act Transparency Statement|Sitemap|About US| Contact US: help@patsnap.com