Manufacturing method for stator
A manufacturing method and stator technology, applied in the manufacture of stator/rotor body, etc., can solve problems such as complex assembly process and reduced stator roundness accuracy, and achieve the effects of simplifying assembly process, increasing slot fullness, and improving winding efficiency
- Summary
- Abstract
- Description
- Claims
- Application Information
AI Technical Summary
Problems solved by technology
Method used
Image
Examples
Embodiment Construction
[0040] In order to make the object, technical solution and advantages of the present invention clearer, the present invention will be further described in detail below in conjunction with the accompanying drawings and embodiments. It should be understood that the specific embodiments described here are only used to explain the present invention, not to limit the present invention.
[0041] like Figure 1~4 and Figures 13 to 18 As shown, the manufacturing method of the stator provided by the embodiment of the present invention includes the following steps:
[0042] Iron core split manufacturing step, respectively manufacturing the first split body 11 and the second split body 12 that can be laminated in the axial direction to form the stator core 1;
[0043] In the winding step, the stator windings are respectively wound on the first split body 11 and the second split body 12, and the first winding coil 201 and the second winding coil 202 are respectively formed on the first s...
PUM
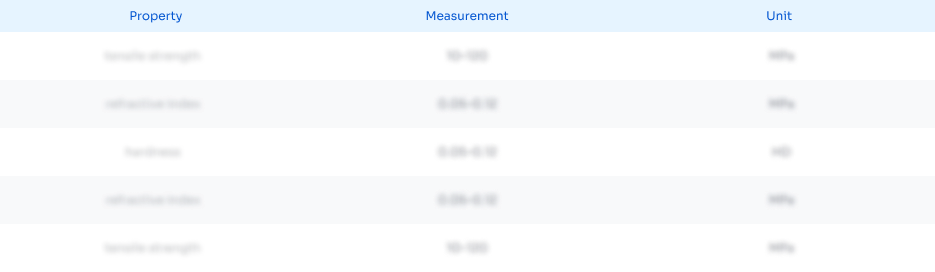
Abstract
Description
Claims
Application Information

- R&D Engineer
- R&D Manager
- IP Professional
- Industry Leading Data Capabilities
- Powerful AI technology
- Patent DNA Extraction
Browse by: Latest US Patents, China's latest patents, Technical Efficacy Thesaurus, Application Domain, Technology Topic, Popular Technical Reports.
© 2024 PatSnap. All rights reserved.Legal|Privacy policy|Modern Slavery Act Transparency Statement|Sitemap|About US| Contact US: help@patsnap.com