Lead acid battery negative grid alloy and preparation method thereof
A technology of lead-acid batteries and lead alloys, which is applied to battery electrodes, circuits, electrical components, etc., and can solve problems such as long aging periods and ineffective effects
- Summary
- Abstract
- Description
- Claims
- Application Information
AI Technical Summary
Problems solved by technology
Method used
Image
Examples
Embodiment 1-5
[0019] Preparation of negative grid alloy:
[0020] A, prepare graphite-lead alloy, make the massfraction of graphite in graphite-lead alloy be 2%~3%;
[0021] b. Add the remaining lead into the lead-melting furnace according to the distribution ratio of the negative grid alloy, heat it to 550-600°C, then add the graphite-lead alloy obtained in step a into the lead-melting furnace and stir evenly, and then put the aluminum The tin alloy is added into the lead-melting furnace, fully melted and stirred evenly to obtain the negative grid alloy.
[0022] After the alloy is prepared, samples are taken to test the composition of the alloy with a direct-reading spectrometer. The main composition should be 0.1% to 0.4% of tin, 0.02% to 0.04% of aluminum, 0.2% to 0.4% of graphite, and the balance is lead. After testing, the composition of the lead-acid battery negative grid alloy prepared in each embodiment is shown in Table 1, and the balance is lead (including unavoidable impurities...
PUM
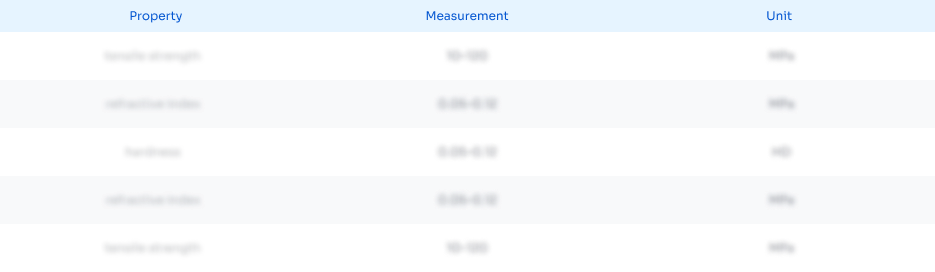
Abstract
Description
Claims
Application Information

- Generate Ideas
- Intellectual Property
- Life Sciences
- Materials
- Tech Scout
- Unparalleled Data Quality
- Higher Quality Content
- 60% Fewer Hallucinations
Browse by: Latest US Patents, China's latest patents, Technical Efficacy Thesaurus, Application Domain, Technology Topic, Popular Technical Reports.
© 2025 PatSnap. All rights reserved.Legal|Privacy policy|Modern Slavery Act Transparency Statement|Sitemap|About US| Contact US: help@patsnap.com