Monolithic catalyst for hydrogen peroxide production through pentylanthraquinone process and preparation method thereof
A monolithic catalyst, amyl anthraquinone technology, applied in chemical instruments and methods, peroxide/peroxyhydrate/peroxyacid/superoxide/ozonide, inorganic chemistry, etc., can solve many factors in the process , complex steps and other issues, to achieve the effects of improving efficiency, easy integration, and simplifying the preparation process
- Summary
- Abstract
- Description
- Claims
- Application Information
AI Technical Summary
Problems solved by technology
Method used
Image
Examples
Embodiment 1
[0052] Preparation of Oxide Slurry
[0053] 20g γ-Al 2 o 3 Mix 60g of nitric acid solution with a concentration of 2wt.% in a 100ml nodular ink tank, adjust the rotational speed of the nodular ink machine to 500r / min, after 16 hours of nodular ink, adjust the pH of the slurry to be between 3-4, and obtain the oxidation catalyst additive Aluminum paste.
[0054] Catalyst preparation
[0055] Select a monolithic catalyst carrier with a pore size of 400 holes / square inch, adopt a conventional impregnation method, and the impregnation time is 3 minutes, then use compressed air to remove excess liquid slurry in the channel of the monolithic catalyst carrier, and then put the monolithic catalyst into the In the muffle furnace, the temperature was raised to 500° C. at a rate of 2° C. / min for 2 hours. Repeat the above-mentioned coating step 3 times, and weigh the weight of the catalyst aid on the coating to be 23% of the overall catalyst carrier.
[0056] 10g PdCl 2 Dissolve in ...
Embodiment 2
[0060] 47.4g Mg(NO 3 ) 2 ·6H 2 After the deionized water of O and 400ml is mixed, move to the constant volume of 500ml in the volumetric flask of 500ml, obtain the Mg of certain concentration (NO 3 ) 2 aqueous solution.
[0061] The preparation process of the oxide slurry and the catalyst is the same as in Example 1. After the monolithic catalyst carrier is coated with the catalyst promoter and roasted, when the weight of the catalyst promoter coated on the carrier is weighed to be 23% of the monolithic catalyst carrier, Then impregnated in the above prepared Mg(NO 3 ) 2 Aqueous solution for 3 minutes, then use compressed air to remove excess liquid in the channels of the monolithic catalyst carrier, and then put the monolithic catalyst into a muffle furnace at a rate of 2 °C / min to 500 °C for 2 hours of calcination.
[0062] The loading method and reduction process of the noble metal active component of the catalyst are the same as in Example 1 to obtain the catalyst Ex...
Embodiment 3
[0064] 49.13g Ba(NO 3 ) 2 ·6H 2 After mixing O and 400ml of deionized water, move it to a volumetric flask of 500ml and set the volume to 500ml to obtain a certain concentration of Ba(NO 3 ) 2 aqueous solution.
[0065] The preparation process of the oxide slurry and the catalyst is the same as in Example 1. After the monolithic catalyst carrier is coated with the catalyst promoter and roasted, when the weight of the catalyst promoter coated on the carrier is weighed to be 23% of the monolithic catalyst carrier, Then impregnated in the above prepared Ba(NO 3 ) 2 Aqueous solution for 3 minutes, then use compressed air to remove excess liquid in the channels of the monolithic catalyst carrier, and then put the monolithic catalyst into a muffle furnace at a rate of 2 °C / min to 500 °C for 2 hours of calcination.
[0066] The loading method and reduction process of the noble metal active component of the catalyst are the same as in Example 1 to obtain the catalyst Exa.3, and ...
PUM
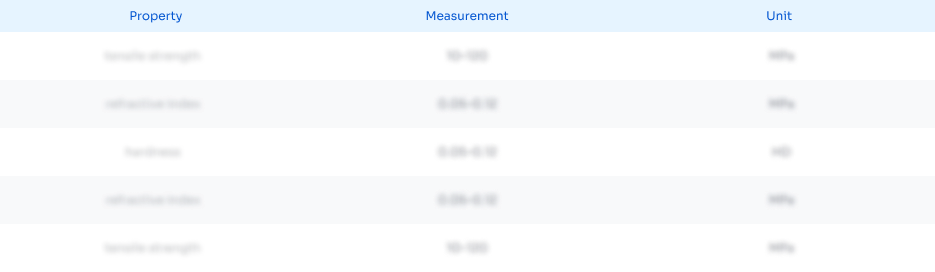
Abstract
Description
Claims
Application Information

- R&D Engineer
- R&D Manager
- IP Professional
- Industry Leading Data Capabilities
- Powerful AI technology
- Patent DNA Extraction
Browse by: Latest US Patents, China's latest patents, Technical Efficacy Thesaurus, Application Domain, Technology Topic, Popular Technical Reports.
© 2024 PatSnap. All rights reserved.Legal|Privacy policy|Modern Slavery Act Transparency Statement|Sitemap|About US| Contact US: help@patsnap.com