Deep dewatering method for sludge
A treatment method and deep dehydration technology, applied in sludge treatment, water/sludge/sewage treatment, dehydration/drying/thickened sludge treatment, etc., can solve the problem of large consumption, high operating cost, and unrealized sludge reduction to achieve the effects of increased particle agglomeration, stable sludge properties, and easy resource utilization
- Summary
- Abstract
- Description
- Claims
- Application Information
AI Technical Summary
Problems solved by technology
Method used
Image
Examples
Embodiment 1
[0028] Using compressed air, waste iron filings, waste sulfuric acid, waste hydrochloric acid to prepare O by reaction 3 , FeCl 3 and Fe 2 (SO 4 ) 3 . In the oxidation and membrane breaking reaction tank composed of two small tanks, 1 ton of residual sludge with a water content of 99.7% was pumped into the first small tank, and 30 g of 98% waste sulfuric acid (pH was controlled at 6.5) and 2 g of O 3 , and stirred for 10 minutes. The sludge mixture enters another small pool, and 50g FeCl is added 3 solution, stirred for 10 minutes. The sludge mixture enters the flocculation reaction tank, and 50g Fe 2 (SO 4 ) 3 Solution, and dosing 2gPAM, stirring reaction for 20 minutes. Then enter the sedimentation tank and let it stand for 30 minutes to allow it to settle and concentrate. Take out the concentrated sludge from the bottom of the sedimentation tank, introduce a plate and frame filter press for dehydration, and keep it under the pressure of 1.2MPa for 40 minutes. Aft...
Embodiment 2
[0030] Using compressed air, waste iron filings, waste sulfuric acid, waste hydrochloric acid to prepare O by reaction 3 , FeCl 3 and Fe 2 (SO 4 ) 3 . In the oxidative membrane breaking reaction tank composed of two small tanks, 1 ton of residual sludge with a water content of 99.7% was pumped into the first small tank, and 30 g of 98% waste sulfuric acid (pH was controlled at 6.5) and 3 g of O 3 , and stirred for 10 minutes. The sludge mixture enters another small pool, and 50g FeCl is added 3 solution, stirred for 10 minutes. The sludge mixture enters the flocculation reaction tank, and 50g Fe 2 (SO 4 ) 3 Solution, and dosing 2gPAM, stirring reaction for 20 minutes. Then enter the sedimentation tank and let it stand for 30 minutes to allow it to settle and concentrate. Take out the concentrated sludge from the bottom of the sedimentation tank, introduce it into a plate and frame filter press for dehydration, and keep it under a pressure of 1.2MPa for 40 minutes. A...
Embodiment 3
[0032] Using compressed air, waste iron filings, waste sulfuric acid, waste hydrochloric acid to prepare O by reaction 3 , FeCl 3 and Fe 2 (SO 4 ) 3 . In the oxidative membrane breaking reaction tank composed of two small tanks, 1 ton of residual sludge with a water content of 99.7% was pumped into the first small tank, and 40 g of 98% waste sulfuric acid (pH was controlled at 6.5) and 4 g of O 3 , and stirred for 10 minutes. The sludge mixture enters another small tank, and 70g FeCl is added 3 solution, stirred for 10 minutes. The sludge mixture enters the flocculation reaction tank, and 70g Fe 2 (SO 4 ) 3 Solution, and dosing 2gPAM, stirring reaction for 20 minutes. Then enter the sedimentation tank and let it stand for 25 minutes to allow it to precipitate and concentrate. Take out the concentrated sludge from the bottom of the sedimentation tank, introduce it into a plate and frame filter press for press filtration and dehydration, keep it under a pressure of 1....
PUM
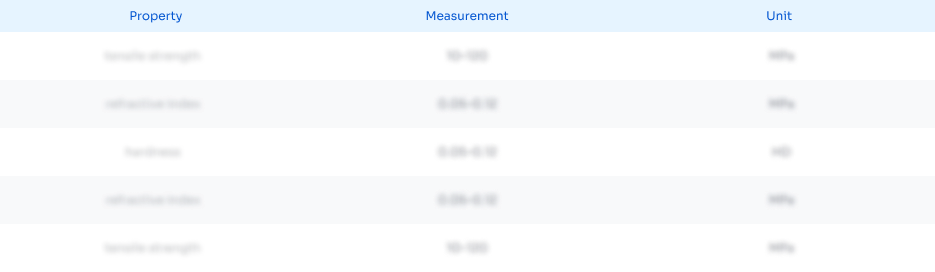
Abstract
Description
Claims
Application Information

- Generate Ideas
- Intellectual Property
- Life Sciences
- Materials
- Tech Scout
- Unparalleled Data Quality
- Higher Quality Content
- 60% Fewer Hallucinations
Browse by: Latest US Patents, China's latest patents, Technical Efficacy Thesaurus, Application Domain, Technology Topic, Popular Technical Reports.
© 2025 PatSnap. All rights reserved.Legal|Privacy policy|Modern Slavery Act Transparency Statement|Sitemap|About US| Contact US: help@patsnap.com