Feeding and unloading device for anti-jump bottle cap molding machine
A molding machine and bottle cap technology, which is applied to household components, household appliances, other household appliances, etc., can solve the problems of increasing equipment costs, falling, and inability to ensure that all rubber materials are blown off, and achieves easy installation and removal. Maintenance , the effect of saving production costs
- Summary
- Abstract
- Description
- Claims
- Application Information
AI Technical Summary
Problems solved by technology
Method used
Image
Examples
Embodiment Construction
[0024] Example: see Figures 3 to 7 As shown, the feeding and unloading device of the anti-jump cap bottle cap molding machine includes the lower cover plate 1, the feeding plate 2 and the cap feeding plate 8 of the bottle cap molding machine, and the lower cover plate 1 and the feeding plate 2 are coaxial. It is fixed on the rotating shaft 3 of the feeding tray, and the scraping nozzle 16 is fixed on the feeding tray 2. A first suction channel 21 is formed on the feeding tray 2, and an air outlet 23 is formed on the first suction channel 21 to allow ventilation. The block 4 is buckled on the feeding tray 2, and the first suction nozzle 5 is formed on the ventilation block 4, and the first suction nozzle 5 is connected with the first suction channel 21, and the ventilation block 4 is inserted and sleeved on the rotating shaft 3 of the feeding tray. On the top, the spring 6 is inserted and sleeved on the feeding disc shaft 3, the nut 7 is screwed on the feeding disc shaft 3, th...
PUM
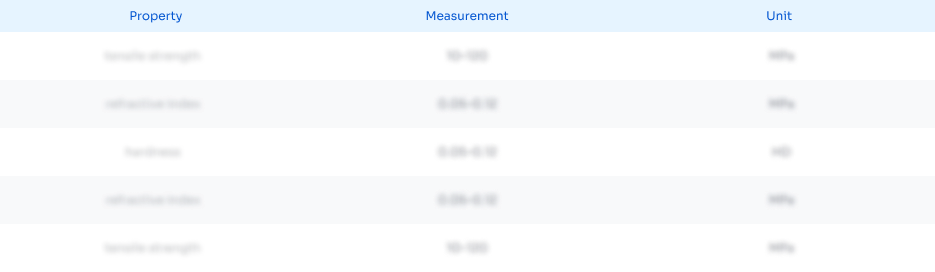
Abstract
Description
Claims
Application Information

- Generate Ideas
- Intellectual Property
- Life Sciences
- Materials
- Tech Scout
- Unparalleled Data Quality
- Higher Quality Content
- 60% Fewer Hallucinations
Browse by: Latest US Patents, China's latest patents, Technical Efficacy Thesaurus, Application Domain, Technology Topic, Popular Technical Reports.
© 2025 PatSnap. All rights reserved.Legal|Privacy policy|Modern Slavery Act Transparency Statement|Sitemap|About US| Contact US: help@patsnap.com