Method for regulating the torque of an induction motor
A technology for asynchronous motors and torque, applied in the control of generators, motor control, motor generator control, etc., can solve problems such as difficult identification
- Summary
- Abstract
- Description
- Claims
- Application Information
AI Technical Summary
Problems solved by technology
Method used
Image
Examples
Embodiment Construction
[0017] figure 1 An example of a traction drive of a rail vehicle is shown. The AC asynchronous electric machine 8 of the rail vehicle is controlled via the traction rectifier 1 with a voltage intermediate circuit inverter. Here, the voltage intermediate circuit 6 of the traction rectifier 1 is brought via the input circuit 5 to the voltage tapped off by the collector / brush 3 between the upper line 2 and the rail 4 . If necessary, the input circuit 5 converts the input voltage into a suitable DC voltage, which is fed to the inverter 7 on the voltage intermediate circuit 6 . The object here is to control the inverter 7 of the traction rectifier 1 with the regulating device 9 in such a way that an alternating voltage with variable amplitude and frequency is generated at the terminals of the asynchronous machine 8 in such a way that the asynchronous machine 8 The desired torque is generated on its shaft 10 both stably and dynamically. Here, under normal circumstances, the limi...
PUM
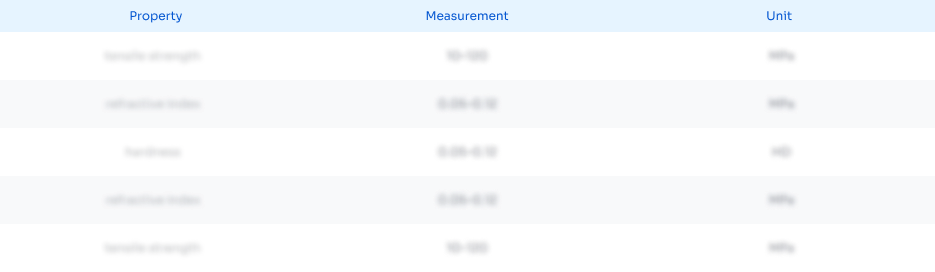
Abstract
Description
Claims
Application Information

- Generate Ideas
- Intellectual Property
- Life Sciences
- Materials
- Tech Scout
- Unparalleled Data Quality
- Higher Quality Content
- 60% Fewer Hallucinations
Browse by: Latest US Patents, China's latest patents, Technical Efficacy Thesaurus, Application Domain, Technology Topic, Popular Technical Reports.
© 2025 PatSnap. All rights reserved.Legal|Privacy policy|Modern Slavery Act Transparency Statement|Sitemap|About US| Contact US: help@patsnap.com