A kind of preparation method of Ni modified thermosetting phenolic resin
A phenolic resin and thermosetting technology, which is applied in the field of Ni-modified thermosetting phenolic resin preparation, can solve the problems of difficult control of pH value and low reaction efficiency, and achieve the effects of saving reaction time, sufficient reaction and stable pH value
- Summary
- Abstract
- Description
- Claims
- Application Information
AI Technical Summary
Problems solved by technology
Method used
Examples
Embodiment 1
[0019] Melt in a 65°C water bath. At 40°C, 1 / 4 of formaldehyde was added dropwise to phenol and basic catalyst NaOH, and an appropriate amount of methanol was added for pre-mixing for 15 minutes. In the process of slowly increasing the temperature to 80°C, continue to drop 1 / 4 of the formaldehyde until the timing starts at 80°C, and react for 1h. Then add the remaining formaldehyde, and react for 2.5h. After the time is up, cool to room temperature, add a mixed solution of oxalic acid and acetic acid to adjust the pH. At 48°C, carry out vacuum distillation until the water output reaches the estimated amount and the experiment ends. A viscous yellowish phenolic resin was obtained.
[0020] In this example, only NaOH was used as the basic catalyst, and NiCl was not added 2 .It was found that in the final product phenolic resin, the content of residual phenol increased greatly and the solid content decreased. It shows that the reaction is not complete, and the reaction rate i...
Embodiment 2
[0022] Melt in a 65°C water bath. At 40°C, in phenol and basic catalysts NaOH and NiCl 2 Add 1 / 4 of formaldehyde to the mixed solution, and add an appropriate amount of methanol for pre-mixing for 15 minutes. In the process of slowly increasing the temperature to 80°C, continue to drop 1 / 4 of the formaldehyde until the timing starts at 80°C, and react for 1h. Then add the remaining formaldehyde, and react for 2.5h. After the time is up, cool to room temperature, add oxalic acid solution, and adjust the pH. At 48°C, carry out vacuum distillation until the water output reaches the estimated amount and the experiment ends. A viscous yellowish phenolic resin was obtained.
[0023] In this embodiment, only the oxalic acid solution was added, and the mixed acid solution of oxalic acid and acetic acid was not added. After the obtained phenolic resin is heated, the degree of degradation is obviously higher than that of the phenolic resin prepared with the mixed acid buffer solutio...
PUM
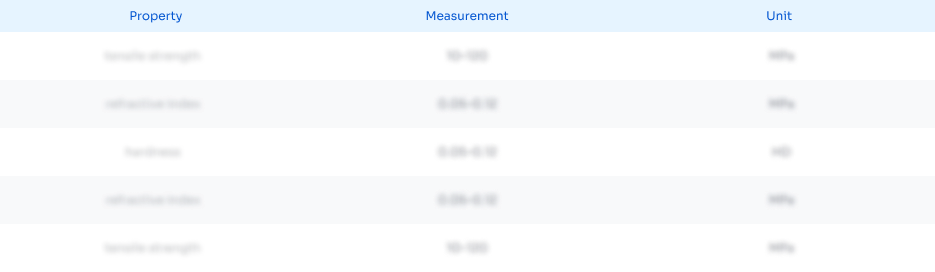
Abstract
Description
Claims
Application Information

- Generate Ideas
- Intellectual Property
- Life Sciences
- Materials
- Tech Scout
- Unparalleled Data Quality
- Higher Quality Content
- 60% Fewer Hallucinations
Browse by: Latest US Patents, China's latest patents, Technical Efficacy Thesaurus, Application Domain, Technology Topic, Popular Technical Reports.
© 2025 PatSnap. All rights reserved.Legal|Privacy policy|Modern Slavery Act Transparency Statement|Sitemap|About US| Contact US: help@patsnap.com