a zro 2 Ceramic particle reinforced molybdenum-based composite material and preparation method thereof
A technology of composite materials and ceramic particles, which is applied in the field of molybdenum-based composite materials, can solve the problems that the high-temperature performance of metal molybdenum and molybdenum alloys cannot meet the use requirements, and achieve easy automatic control, good comprehensive performance and high-temperature mechanical properties, and simple process Effect
- Summary
- Abstract
- Description
- Claims
- Application Information
AI Technical Summary
Problems solved by technology
Method used
Image
Examples
Embodiment 1
[0024] The ZrO of this embodiment 2 The ceramic particle reinforced molybdenum-based composite material is made of the following raw materials: 1.74g of zirconium nitrate pentahydrate, 91.04g of ammonium dimolybdate, and 136.56g of citric acid.
[0025] The ZrO of this embodiment 2 The preparation method of ceramic particle reinforced molybdenum-based composite material comprises the following steps:
[0026] 1) Take 91.04g of ammonium dimolybdate to prepare an aqueous solution with a mass concentration of 25%, take 136.56g of citric acid to prepare an aqueous solution with a mass concentration of 30%, and take 1.74g of zirconium nitrate pentahydrate to prepare a mass concentration of zirconium nitrate It is a 35% aqueous solution. Add zirconium nitrate aqueous solution to ammonium dimolybdate aqueous solution to produce a white precipitate, then add citric acid aqueous solution, and the white precipitate disappears to form a transparent mixed solution. Add nitric acid or amm...
Embodiment 2
[0031] The ZrO of this embodiment 2 The ceramic particle reinforced molybdenum-based composite material is made of the following raw materials: 8.72g of zirconium nitrate pentahydrate, 87.36g of ammonium dimolybdate, and 131.05g of citric acid.
[0032] The ZrO of this embodiment 2 The preparation method of ceramic particle reinforced molybdenum-based composite material comprises the following steps:
[0033] 1) Take 91.04g of ammonium dimolybdate to prepare an aqueous solution with a mass concentration of 30%, take 136.56g of citric acid to prepare an aqueous solution with a mass concentration of 35%, and take 8.72g of zirconium nitrate pentahydrate to prepare a mass concentration of zirconium nitrate It is a 25% aqueous solution. Add zirconium nitrate aqueous solution to ammonium dimolybdate aqueous solution to produce a white precipitate, then add citric acid aqueous solution, and the white precipitate disappears to form a transparent mixed solution. Add nitric acid or amm...
Embodiment 3
[0038] The ZrO of this embodiment 2 The ceramic particle reinforced molybdenum-based composite material is made of the following raw materials: 17.44g of zirconium nitrate pentahydrate, 82.76g of ammonium dimolybdate, and 124.15g of citric acid.
[0039] The ZrO of this embodiment 2 The preparation method of ceramic particle reinforced molybdenum-based composite material comprises the following steps:
[0040] 1) Take 82.76g of ammonium dimolybdate to prepare an aqueous solution with a mass concentration of 35%, take 124.15g of citric acid to prepare an aqueous solution with a mass concentration of 25%, and take 17.44g of zirconium nitrate pentahydrate to prepare a mass concentration of zirconium nitrate It is a 30% aqueous solution. Add nitric acid or ammonia water dropwise to the ammonium dimolybdate aqueous solution to adjust its pH to 1. Add the zirconium nitrate aqueous solution to the ammonium dimolybdate aqueous solution to produce a white precipitate, then add citric ...
PUM
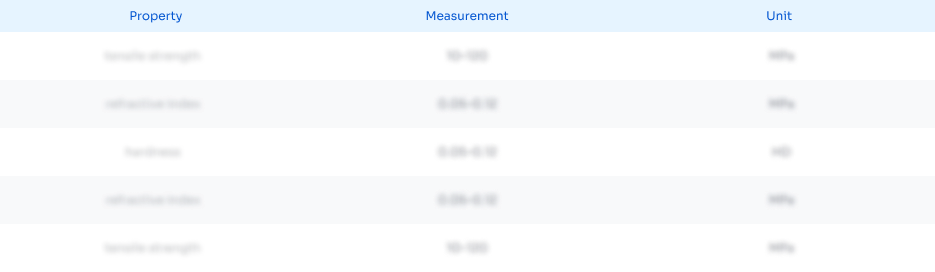
Abstract
Description
Claims
Application Information

- Generate Ideas
- Intellectual Property
- Life Sciences
- Materials
- Tech Scout
- Unparalleled Data Quality
- Higher Quality Content
- 60% Fewer Hallucinations
Browse by: Latest US Patents, China's latest patents, Technical Efficacy Thesaurus, Application Domain, Technology Topic, Popular Technical Reports.
© 2025 PatSnap. All rights reserved.Legal|Privacy policy|Modern Slavery Act Transparency Statement|Sitemap|About US| Contact US: help@patsnap.com