Descaling cleaning agent for poly-containing dirt on polymer flooding produced liquid treatment equipment
A cleaning agent and liquid treatment technology, which is applied in the direction of detergent compounding agent, detergent composition, surface active detergent composition, etc., can solve the problem of serious accumulation of dirt in production liquid treatment equipment, and achieve the goal of being suitable for marine transportation and Long-term storage, stable performance, and the effect of enhancing solvency
- Summary
- Abstract
- Description
- Claims
- Application Information
AI Technical Summary
Problems solved by technology
Method used
Examples
Embodiment 1
[0018] Take 60.73g of the dirt-containing sample attached to the electric dehydrator and put it in a 250ml beaker, and prepare 100g of descaling and cleaning agent with on-site formation water, and the proportion is:
[0019] 6% N-methylmorpholine;
[0020] 4% sodium tert-butoxide;
[0021] 5% Triethanolamine Lauryl Phosphate;
[0022] 22% Alkylphenol Ethoxylates;
[0023] 8% Sodium Alkyl Sulfate Ethoxylate;
[0024] 16% propylene glycol;
[0025] 14% isopropanol;
[0026] 14% propylene glycol butyl ether;
[0027] 0.8% sodium tripolyphosphate;
[0028] 2.5% EDTA tetrasodium salt;
[0029] 0.8% diethylenetriaminepentaacetate;
[0030] The remainder is water;
[0031] The dirt and scale samples on the electric dehydrator were completely dispersed after soaking in the descaling and cleaning agent at room temperature for 4 hours, and there was no agglomerated scale in the solution, which indicated that the dirt and scale samples containing polymers had been completely di...
Embodiment 2
[0033] Take 65.58g of the dirt-containing sample attached to the electric dehydrator and put it in a 250ml beaker, prepare 100g of descaling and cleaning agent with the formation water on site, and the proportion is:
[0034] 7% N,N-Diisopropylethylamine;
[0035] 5% Triethanolamine Lauryl Phosphate;
[0036] 5% sodium hydroxymethylcellulose;
[0037] 22% cetyl alcohol polyoxyethylene ether;
[0038] 9% myristyl polyoxyethylene ether succinate monoester sulfonate;
[0039] 17% ethylene glycol;
[0040] 13% ethylene glycol dimethyl ether;
[0041] 10% isopropanol;
[0042] 0.4% potassium pyrophosphate;
[0043] 1.2% sodium citrate;
[0044] 0.6% sodium alpha-glucoheptonate;
[0045] The remainder is water;
[0046] The dirt and scale samples on the electric dehydrator were completely dispersed after soaking in the descaling and cleaning agent at room temperature for 4 hours, and there was no agglomerated scale in the solution, which indicated that the dirt and scale sa...
Embodiment 3
[0048] Take 49.82g of the dirt-containing sample attached to the electric dehydrator and put it in a 250ml beaker, prepare 100g of descaling and cleaning agent with on-site formation water, and the mass percentages of each component in the descaling and cleaning agent are:
[0049] 8% N,N-Diisopropylethylamine;
[0050] 4% 1,8-diazabicycloundec-7-ene;
[0051] 6% sodium hydroxymethylcellulose;
[0052] 20% alkylphenol polyoxyethylene ether;
[0053] 8% Sodium Alkyl Sulfate Ethoxylate;
[0054] 20% propylene glycol;
[0055] 10% isopropanol;
[0056] 10% propylene glycol butyl ether;
[0057] 0.3% sodium tripolyphosphate;
[0058] 1.2% EDTA tetrasodium salt;
[0059] 0.5% diethylenetriaminepentaacetate;
[0060] The remainder is water;
[0061] The dirt and scale samples on the electric dehydrator were completely dispersed after soaking in the descaling and cleaning agent at room temperature for 4 hours, and there was no agglomerated scale in the solution, which indica...
PUM
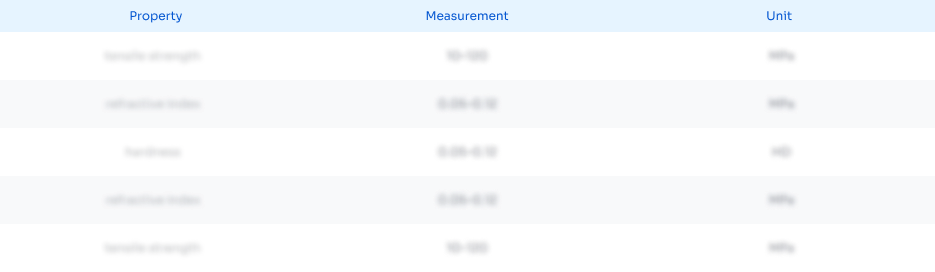
Abstract
Description
Claims
Application Information

- Generate Ideas
- Intellectual Property
- Life Sciences
- Materials
- Tech Scout
- Unparalleled Data Quality
- Higher Quality Content
- 60% Fewer Hallucinations
Browse by: Latest US Patents, China's latest patents, Technical Efficacy Thesaurus, Application Domain, Technology Topic, Popular Technical Reports.
© 2025 PatSnap. All rights reserved.Legal|Privacy policy|Modern Slavery Act Transparency Statement|Sitemap|About US| Contact US: help@patsnap.com