Tandem continuous ball mill and ball milling method
A continuous ball milling and tandem technology, used in grain processing and other directions, can solve the problems of low ball milling output, poor adjustability, and low production efficiency, and achieve the effect of improving work efficiency and grinding effect, improving overall pressure and improving grinding efficiency.
- Summary
- Abstract
- Description
- Claims
- Application Information
AI Technical Summary
Problems solved by technology
Method used
Image
Examples
Embodiment 1
[0040] Such as figure 1 , 2 As shown: the feeding device 1 is an independent transmission unit, which is at the forefront of the entire tandem continuous ball mill. The first-stage ball mill tank 4 and the independent transmission device 2 form a first-stage ball mill unit with independent transmission. The second-stage ball mill tank 7 and the independent The transmission device 2 constitutes a two-stage ball mill unit with independent transmission. The feeding device delivery cylinder 107 is inserted into the feed end cover of the primary ball mill tank 4 of the ball mill. The primary ball mill tank 4 and the adjacent secondary ball mill tank 7 They are connected through the connection device 3, the secondary ball milling tank has three stages, and the adjacent secondary ball milling tanks 7 are connected through the connection device 3, and the connection device 3 is responsible for supplying the secondary ball milling tank 7 without stopping the machine. Add grinding ball...
Embodiment 2
[0058] When the particle size of the material is relatively low, you can choose to connect two secondary ball milling pots 7 behind the primary ball milling pot 4. The length of the primary ball milling pot 4 is 15m, and the length of the secondary ball milling pot 7 is 5m. The structure remains unchanged, and the assembly method and ball milling method are as in Example 1.
Embodiment 3
[0060] If the material requirements are high, you can choose to connect multiple secondary ball milling pots 7 behind the primary ball milling pot 4. The specific number of stages is selected according to actual needs. It is 8m, and the other structural shapes are unchanged, and the assembly method and ball milling method are as in Example 1.
PUM
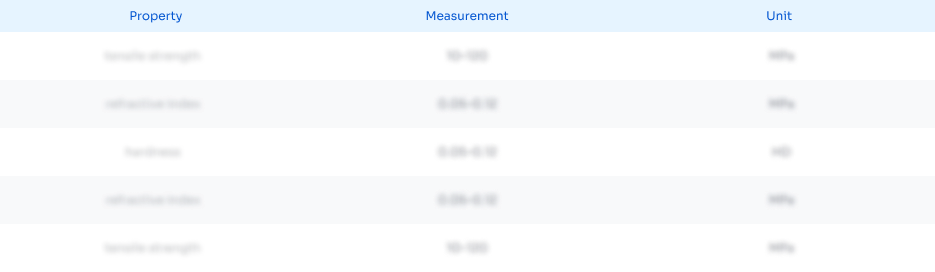
Abstract
Description
Claims
Application Information

- R&D
- Intellectual Property
- Life Sciences
- Materials
- Tech Scout
- Unparalleled Data Quality
- Higher Quality Content
- 60% Fewer Hallucinations
Browse by: Latest US Patents, China's latest patents, Technical Efficacy Thesaurus, Application Domain, Technology Topic, Popular Technical Reports.
© 2025 PatSnap. All rights reserved.Legal|Privacy policy|Modern Slavery Act Transparency Statement|Sitemap|About US| Contact US: help@patsnap.com