Novel high-throughput micro-channel reactor provided with multiple layers of spirally winding tubes
A micro-channel reactor and high-throughput technology, applied in the field of new high-throughput multi-layer spiral wound tube micro-channel reactors, can solve the problems of uneven mixing of the reactor, high processing cost, unfavorable industrial amplification, etc., and achieve high efficiency The effect of continuous safety production, saving reaction time and saving R&D costs
- Summary
- Abstract
- Description
- Claims
- Application Information
AI Technical Summary
Problems solved by technology
Method used
Image
Examples
Embodiment 1
[0029] The novel high-throughput multi-layer spiral wound tube microchannel reactor that the embodiment of the present invention proposes, see figure 1 , mainly including reactant inlet and outlet sections 1a, 1b, inlet and outlet heads 2a, 2b, flanges 3a, 3b, inlet and outlet tube plates 4a, 4b, stainless steel capillary 5, fixed gasket 6, cylinder 7 , Around the cylinder 8, constant temperature medium inlet and outlet sections 9a, 9b, baffles 10a, 10b, left and right support 11a, 11b, center support tube 12, support 13.
[0030] Specifically, see figure 2 The two ends of the central support tube 12 are connected to the inlet and outlet tube plates 4a and 4b by welding to ensure the rigidity of the entire reactor. The support member 13 is connected by welding, and the inlet and outlet tube plates 4a, 4b, the central support tube 12, the winding cylinder 8 and the support member 13 constitute the supporting framework of the spiral wound tube microchannel reactor.
[0031] T...
Embodiment 2
[0043] The present invention also provides a kind of esterification technological process utilizing the helical winding tube microchannel reactor in embodiment 1 to synthesize diethyl methyl ester, see Figure 4 , involving two high-level liquid tanks respectively equipped with methanol + catalyst mixed liquid and diketene, two explosion-proof metering pumps, static mixer, spiral wound tube microchannel reactor, extension tube, constant temperature water bath, ice water bath, temperature measurement A pressure measuring instrument and connecting components including an explosion-proof electric ball valve, a check valve, an explosion-proof membrane, and an explosion-proof flowmeter. After being pumped into the static mixer and the check valve, the reaction solution is fully mixed. After mixing, it is quickly passed into the spiral-wound tube microchannel reactor. The reaction is fully carried out in the stainless steel capillary of the spiral-wound tube microchannel reactor. Th...
PUM
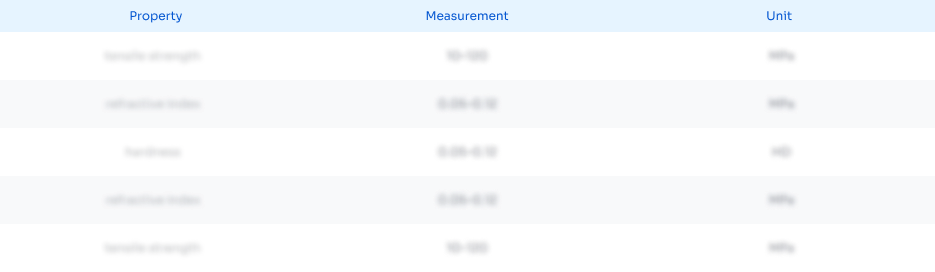
Abstract
Description
Claims
Application Information

- Generate Ideas
- Intellectual Property
- Life Sciences
- Materials
- Tech Scout
- Unparalleled Data Quality
- Higher Quality Content
- 60% Fewer Hallucinations
Browse by: Latest US Patents, China's latest patents, Technical Efficacy Thesaurus, Application Domain, Technology Topic, Popular Technical Reports.
© 2025 PatSnap. All rights reserved.Legal|Privacy policy|Modern Slavery Act Transparency Statement|Sitemap|About US| Contact US: help@patsnap.com