Method for producing methane and co-producing liquid fuel from carbonaceous material
A liquid fuel, carbonaceous technology, applied in the field of indirect conversion of carbonaceous materials, can solve the problems of increasing energy consumption, low catalyst efficiency, reducing carbon use efficiency, etc., to save energy consumption, low equipment utilization, and improve carbon utilization. rate effect
- Summary
- Abstract
- Description
- Claims
- Application Information
AI Technical Summary
Problems solved by technology
Method used
Image
Examples
Embodiment 1
[0050] This example is used to illustrate the method for producing methane cogeneration liquid fuel from carbonaceous materials provided by the present invention.
[0051]Lignite fragments with a particle size of 5-50 mm (see Table 1 for chemical composition) are gasified into crude synthesis gas with oxygen / water vapor as a gasification agent, and the obtained crude synthesis gas is sequentially cooled, detarred, crude desulfurized, After the fine desulfurization process, the net syngas (see Table 2 for the composition) is obtained, in which (CO+H 2 ) content is 63% by volume, H 2 / CO molar ratio is 1.59;
[0052] The net synthesis gas is divided into two streams, G1 and G2. Among them, G1 is sent to the Fischer-Tropsch synthesis reactor after heat exchange and temperature rise, and is mixed with a precipitated iron catalyst (composition: 94% by weight Fe 2 o 3 -5 wt%CuO-1 wt%K 2 O, the specific surface area after reduction is 168m 2 / g) contact reaction to obtain the co...
Embodiment 2
[0056] The preparation and composition of the net synthesis gas was the same as in Example 1. The entirety of this net synthesis gas is divided into two streams G1 and G2. Among them, G1 is sent to the fixed fluidized bed Fischer-Tropsch synthesis reactor after heat exchange and temperature rise, and is mixed with molten iron catalyst (Fe 2 o 3 The content is 99.6% by weight, the particle size is 20-40 mesh) contact reaction. Among them, the inlet temperature of the Fischer-Tropsch synthesis reactor is 320°C, the outlet temperature is 348°C, the pressure is 2.72MPa, and the gas space velocity is 700h -1 . The reacted product is cooled to 40°C by indirect heat exchange and divided into gas stream G f and liquid stream L f Two parts (see Table 3 for the weight ratio), in the gas stream (H 2 +CO) content of 49% by volume, H 2 / CO molar ratio is 3.94;
[0057] G2 is sent to the water-gas shift reactor after heat exchange. The catalyst is Co-Mo catalyst (manufactured by Qin...
Embodiment 3
[0060] The preparation and composition of the net synthesis gas was the same as in Example 1. The entirety of this net synthesis gas is divided into two streams G1 and G2. Among them, G1 is sent to the fixed-bed Fischer-Tropsch synthesis reactor after heat exchange and temperature rise, and is mixed with the precipitated catalyst (composition: 96% by weight Fe 2 o 3 -3 wt%CuO-1 wt%K 2 O, the specific surface area after reduction is 145m 2 / g) contact reaction. Among them, the inlet temperature of the Fischer-Tropsch synthesis reactor is 239°C, the outlet temperature is 252°C, the pressure is 2.89MPa, and the gas space velocity is 2000h -1 . The reacted product is cooled to 40°C by indirect heat exchange and divided into gas stream G f and liquid stream L f Two parts (see Table 3 for the weight ratio), in the gas stream (H 2 +CO) content of 61% by volume, H 2 / CO molar ratio is 1.98;
[0061] G2 is sent to the water-gas shift reactor after heat exchange, the catalyst ...
PUM
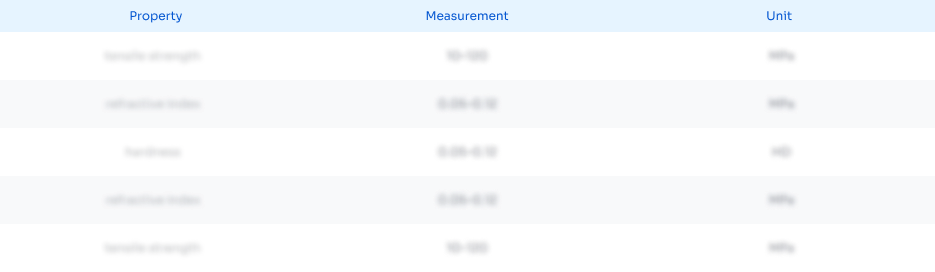
Abstract
Description
Claims
Application Information

- R&D Engineer
- R&D Manager
- IP Professional
- Industry Leading Data Capabilities
- Powerful AI technology
- Patent DNA Extraction
Browse by: Latest US Patents, China's latest patents, Technical Efficacy Thesaurus, Application Domain, Technology Topic, Popular Technical Reports.
© 2024 PatSnap. All rights reserved.Legal|Privacy policy|Modern Slavery Act Transparency Statement|Sitemap|About US| Contact US: help@patsnap.com