Heat-resistant modified polypropylene film master batch and preparation method thereof
A polypropylene film and heat-resistant modification technology, applied in the field of heat-resistant modified polypropylene film masterbatch and its preparation, can solve the problems of poor heat resistance, easy shrinkage and deformation, etc., and achieve good heat resistance and excellent resistance. thermal effect
- Summary
- Abstract
- Description
- Claims
- Application Information
AI Technical Summary
Problems solved by technology
Method used
Examples
Embodiment 1
[0012] Heat-resistant modified polypropylene film masterbatch, including the following raw materials in parts by mass: 78 parts of polypropylene, 18 parts of linear low-density polyethylene, 1 part of light calcium carbonate, 0.4 part of oxidized polyethylene, tert-butyl hydroquinone 0.6 parts.
[0013] The preparation method of this example includes the following steps: weighing each raw material according to the mass ratio, stirring and mixing them evenly in a high-speed mixer, and then placing the mixed materials in a twin-screw extruder, controlling the temperature of each section to 180°C, extruding After granulation, the heat-resistant modified polypropylene film masterbatch is obtained.
[0014] The finished product obtained in this embodiment is tested for performance, and the test results are shown in Table 1.
Embodiment 2
[0016] Heat-resistant modified polypropylene film master batch, including the following raw materials in parts by mass: 80 parts of polypropylene, 21 parts of linear low-density polyethylene, 3 parts of light calcium carbonate, 0.6 parts of oxidized polyethylene, tert-butyl hydroquinone 0.8 servings.
[0017] The preparation method of this example includes the following steps: weigh each raw material according to the mass ratio, stir and mix them evenly in a high-speed mixer, and then place the mixed materials in a twin-screw extruder, control the temperature of each section to 190°C, and extrude After granulation, the heat-resistant modified polypropylene film masterbatch is obtained.
[0018] The finished product obtained in this embodiment is tested for performance, and the test results are shown in Table 1.
Embodiment 3
[0020] Heat-resistant modified polypropylene film masterbatch, including the following raw materials in parts by mass: 79 parts of polypropylene, 20 parts of linear low-density polyethylene, 2 parts of light calcium carbonate, 0.5 parts of oxidized polyethylene, tert-butylhydroquinone 0.7 parts.
[0021] The preparation method of this example includes the following steps: weigh each raw material according to the mass ratio, stir and mix them evenly in a high-speed mixer, and then place the mixed materials in a twin-screw extruder, control the temperature of each section to 190°C, and extrude After granulation, the heat-resistant modified polypropylene film masterbatch is obtained.
[0022] The finished product obtained in this embodiment is tested for performance, and the test results are shown in Table 1.
[0023]
[0024] Embodiment 1-3 gained finished product is carried out performance test, and the results are shown in the following table 1:
[0025] Table 1 Performance...
PUM
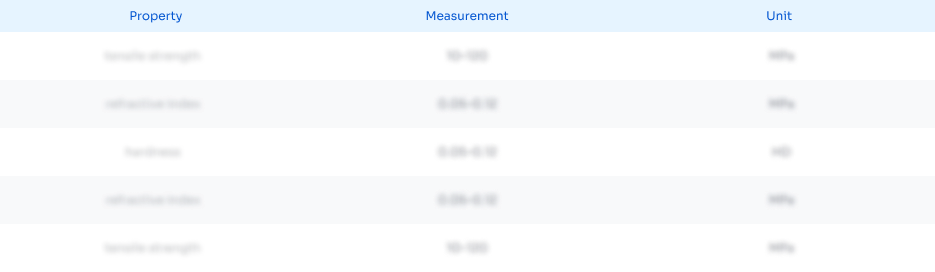
Abstract
Description
Claims
Application Information

- Generate Ideas
- Intellectual Property
- Life Sciences
- Materials
- Tech Scout
- Unparalleled Data Quality
- Higher Quality Content
- 60% Fewer Hallucinations
Browse by: Latest US Patents, China's latest patents, Technical Efficacy Thesaurus, Application Domain, Technology Topic, Popular Technical Reports.
© 2025 PatSnap. All rights reserved.Legal|Privacy policy|Modern Slavery Act Transparency Statement|Sitemap|About US| Contact US: help@patsnap.com