Regeneration method of butene oxidative dehydrogenation catalyst
A technology of oxidative dehydrogenation and catalyst, which is applied in the direction of catalyst regeneration/reactivation, metal/metal oxide/metal hydroxide catalyst, physical/chemical process catalyst, etc. It can solve the problem of shortened service life, long induction period, and decreased activity And other issues
- Summary
- Abstract
- Description
- Claims
- Application Information
AI Technical Summary
Problems solved by technology
Method used
Image
Examples
Embodiment 1
[0024] In a 1.5-liter adiabatic two-stage reactor, the iron-based spinel oxidative dehydrogenation catalyst was used, the conversion rate was 78.5%, and the selectivity was 92.6%. After the catalyst was used for 4000 hours, the conversion rate dropped to 73.2%, and the selectivity 90.4%.
[0025] At 440°C, oxygen / water vapor volume ratio = 0.03, water vapor volume space velocity 1200h -1 Carry out charcoal burning under the same conditions, and after 8 hours, the bed temperature will no longer drop; then control the reaction temperature to 380°C, the oxygen / water vapor volume ratio to 0.03, and the water vapor volume space velocity to 800h -1 , dimethyl disulfide concentration of 20ppm, and system pressure of 0.1MPa for 60 hours. The specific treatment conditions are shown in Table 1.
[0026] Stop the feeding of dimethyl disulfide, wait until the system reaches the reaction conditions, the butene feed starts to react, at 380°C, the volume space velocity of butene is 400 hour...
Embodiment 2
[0029] The catalyst after deactivation is the same as [Example 1], at 380°C, oxygen / water vapor volume ratio=0.04, water vapor volume space velocity 600h -1 Carry out charcoal burning under the same conditions, and after 6 hours, the bed temperature will no longer drop; then control the reaction temperature to 340°C, the oxygen / water vapor volume ratio to 0.05, and the water vapor volume space velocity to 1600h -1 , Methyl ethyl disulfide concentration 10ppm, system pressure 0.05MPa condition and process 70 hours, all the other are the same as [embodiment 1].
[0030]
Embodiment 3
[0032] The catalyst after deactivation is the same as [Example 1], at 380°C, oxygen / water vapor volume ratio=0.05, water vapor volume space velocity 800h -1 Carry out charcoal burning under the same conditions, and after 5 hours, the bed temperature will no longer drop; then control the reaction temperature to 420°C, the oxygen / water vapor volume ratio to 0.03, and the water vapor volume space velocity to 1600h -1 , dimethyl disulfide concentration 50ppm, system pressure 0.15MPa under the conditions of 72 hours, all the other with [embodiment 1].
[0033]
PUM
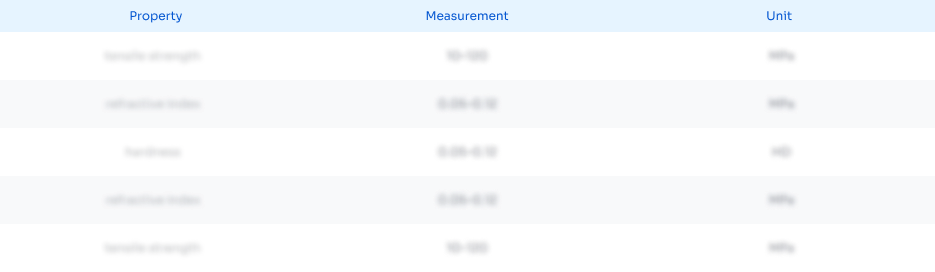
Abstract
Description
Claims
Application Information

- R&D Engineer
- R&D Manager
- IP Professional
- Industry Leading Data Capabilities
- Powerful AI technology
- Patent DNA Extraction
Browse by: Latest US Patents, China's latest patents, Technical Efficacy Thesaurus, Application Domain, Technology Topic, Popular Technical Reports.
© 2024 PatSnap. All rights reserved.Legal|Privacy policy|Modern Slavery Act Transparency Statement|Sitemap|About US| Contact US: help@patsnap.com