Catalyst for direct preparation of low carbon olefin from synthesis gas and preparation method thereof
A low-carbon olefin and catalyst technology, which is applied to the catalyst for the direct preparation of low-carbon olefins from synthesis gas and the field of preparation thereof, can solve the problems of easy flying temperature, low weight selectivity of low-carbon olefins, difficult reaction heat removal and the like
- Summary
- Abstract
- Description
- Claims
- Application Information
AI Technical Summary
Problems solved by technology
Method used
Image
Examples
Embodiment 1
[0022] Get 606.03g of iron nitrate nonahydrate and 3.13g of gallium nitrate nonahydrate and dissolve in water to make solution I; 1076g of 50% manganese nitrate and 0.36g of titanium sulfate are dissolved in water to make solution, and then this solution is mixed with 414.1 A solution made of solid potassium carbonate of g is co-currently precipitated, and the precipitate is filtered and washed repeatedly with deionized water to remove excess impurity ions to obtain fresh and clean mixed precipitate II of manganese carbonate and titanium carbonate, and the solution I and The mixed precipitate II was mixed and beaten to obtain colloidal slurry III; 242.7g magnesium nitrate hexahydrate was dissolved in water to make a solution, and then the solution was co-flowed with 330g of 10% by weight ammonia water to precipitate, filter and wash to obtain fresh magnesium oxide precipitate, Add the magnesium oxide precipitate and 8.4g potassium hydroxide to the slurry III, mix and beat, and ...
Embodiment 2
[0026]The ferric nitrate nonahydrate of 606.03g and the gallium nitrate nonahydrate of 313.3g are dissolved in water and made into solution I; The manganese nitrate of 2.69g 50% and the titanium sulfate of 108g are dissolved in water and make solution, then this solution and 125.3 A solution made of solid potassium carbonate of 2 g is co-currently precipitated, and the precipitate is filtered and washed repeatedly with deionized water to remove excess impurity ions to obtain fresh and clean mixed precipitate II of manganese carbonate and titanium carbonate, and the solution I and The mixed precipitate II was mixed and beaten to obtain colloidal slurry III; 161.7g magnesium nitrate hexahydrate was dissolved in water to make a solution, and then the solution was co-flowed with 220g of 10% by weight ammonia water to precipitate, filter and wash to obtain fresh magnesium oxide precipitate, Add the magnesium oxide precipitate and 0.084g potassium hydroxide to the slurry III, mix and...
Embodiment 3
[0030] Get 367.43g ferric citrate and 313.3g gallium nitrate nonahydrate and dissolve in water to make solution I; 2.69g 50% manganese nitrate and 108g titanium sulfate are dissolved in water to make solution, then this solution is mixed with 125.3g A solution made of solid potassium carbonate is co-currently precipitated. The precipitate is filtered and washed repeatedly with deionized water to remove excess impurity ions to obtain a fresh and clean mixed precipitate II of manganese carbonate and titanium carbonate. The solution I is mixed with Precipitate II was mixed and beaten to obtain colloidal slurry III; 3395.7g magnesium nitrate hexahydrate was dissolved in water to make a solution, and then the solution was mixed with 4620g of 10% by weight ammonia water to precipitate, filter and wash to obtain fresh magnesium oxide precipitate. The magnesium oxide precipitate and 0.084g potassium hydroxide were added to the slurry III, mixed and beaten, and the pH value of the slurr...
PUM
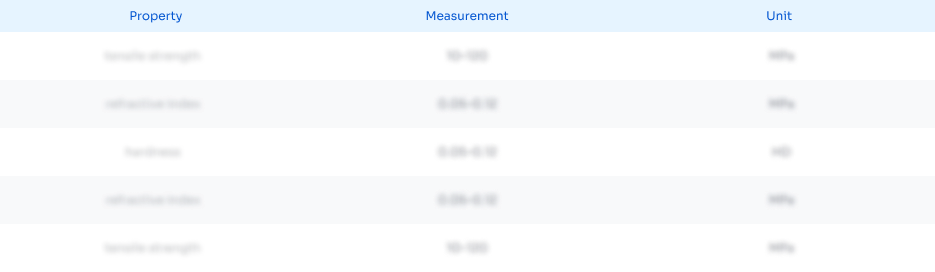
Abstract
Description
Claims
Application Information

- R&D
- Intellectual Property
- Life Sciences
- Materials
- Tech Scout
- Unparalleled Data Quality
- Higher Quality Content
- 60% Fewer Hallucinations
Browse by: Latest US Patents, China's latest patents, Technical Efficacy Thesaurus, Application Domain, Technology Topic, Popular Technical Reports.
© 2025 PatSnap. All rights reserved.Legal|Privacy policy|Modern Slavery Act Transparency Statement|Sitemap|About US| Contact US: help@patsnap.com