Gearbox arrangement for a rail vehicle
A technology for rail vehicles and gearboxes, applied to transmission parts, transmissions driven by electric motors, gear lubrication/cooling, etc., to achieve the effect of good lubricant supply
- Summary
- Abstract
- Description
- Claims
- Application Information
AI Technical Summary
Problems solved by technology
Method used
Image
Examples
Embodiment Construction
[0014] figure 1 and figure 2 A possible embodiment variant of a transmission gearbox arrangement for a rail vehicle is shown by way of example. The transmission gearbox arrangement can be embodied, for example, as an axle transmission gearbox of a rail vehicle.
[0015] by figure 1 It can be seen in the sectional view that the drive pinion 1 , which is formed in one piece with the drive shaft, meshes with the output gear 2 , which is larger in terms of outer diameter, as a helical spur gear. The output gear 2 is connected to an output shaft 3 designed as a hollow shaft. The drive pinion 1 and the driven gear 2 are supported in the transmission gearbox housing 4 via cylindrical roller bearings 5 , 5A. In the lower part of the transmission gearbox housing 4 there is provided a bottom oil pan 6 for lubricant supply to the driven gear 2 into which the teeth of the driven gear 2 sink.
[0016] In the embodiment variant shown by way of example, several thrust rings are provi...
PUM
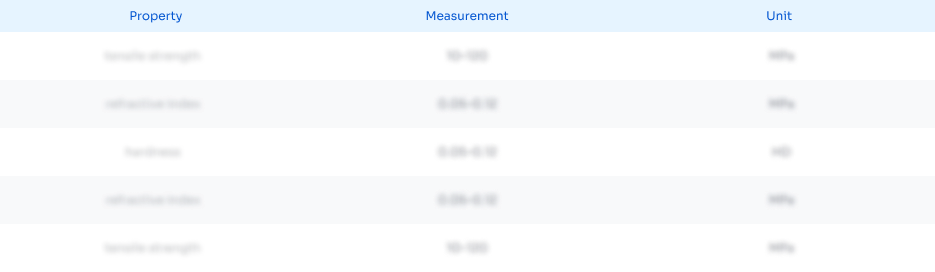
Abstract
Description
Claims
Application Information

- R&D
- Intellectual Property
- Life Sciences
- Materials
- Tech Scout
- Unparalleled Data Quality
- Higher Quality Content
- 60% Fewer Hallucinations
Browse by: Latest US Patents, China's latest patents, Technical Efficacy Thesaurus, Application Domain, Technology Topic, Popular Technical Reports.
© 2025 PatSnap. All rights reserved.Legal|Privacy policy|Modern Slavery Act Transparency Statement|Sitemap|About US| Contact US: help@patsnap.com