A method for plasma texturing of azo thin films for thin film solar cells
A solar cell and plasma technology, applied in circuits, photovoltaic power generation, electrical components, etc., can solve the problems of insignificant texture effect, limited particle energy, environmental pollution, etc., to improve the light trap effect and improve the controllability Effect
- Summary
- Abstract
- Description
- Claims
- Application Information
AI Technical Summary
Problems solved by technology
Method used
Image
Examples
Embodiment 1
[0035] For the AZO glass substrate, first rinse with decontamination powder and water until there are no air bubbles; then rinse with acetone, then rinse with 95% ethanol, and ultrasonically clean with ethanol solution for 20 minutes; finally rinse with deionized water, and use Ultrasonic cleaning with deionized water for 20 minutes, and then drying with high-purity nitrogen, set aside.
[0036] Send the cleaned AZO glass substrate to the sampling chamber, and send the substrate to the substrate holder in the reaction chamber of the plasma etching device through the sampling chamber; turn on the heating power supply, heat the substrate holder, and keep heating The temperature is 200°C; the vacuum of the reaction chamber is evacuated to 1.5×10 -4 Pa; Introduce nitrogen and hydrogen, the flow rates are 8sccm and 2.5sccm respectively; adjust the working pressure of the reaction chamber to keep it at 3Pa; turn on the radio frequency power supply, preheat for 5 minutes, set the fre...
Embodiment 2
[0039] The cleaning of the AZO glass substrate adopts the method of embodiment one; the AZO glass substrate cleaned up is sent to the sample introduction chamber, and the substrate is sent to the substrate holder of the reaction chamber of the plasma etching device through the sample introduction chamber; Heating the power supply, heating the substrate rack, and keeping the heating temperature at 200°C; pumping the vacuum of the reaction chamber to 1.5×10 -4 Pa; Introduce nitrogen and hydrogen, the flow rates are 8sccm and 2.5sccm respectively; adjust the working pressure of the reaction chamber to keep it at 3Pa; turn on the radio frequency power supply, preheat for 5 minutes, set the frequency and power to 456KHz and 1800W respectively; adjust the radio frequency Match until the ignition generates plasma; continue to feed the above-mentioned nitrogen and hydrogen, and keep heating the substrate holder at 200 ° C, and start timing at the same time; after 10 minutes, turn off t...
Embodiment 3
[0042]The cleaning of the AZO glass substrate adopts the method of embodiment one; the AZO glass substrate cleaned up is sent to the sample introduction chamber, and the substrate is sent to the substrate holder of the reaction chamber of the plasma etching device through the sample introduction chamber; Heating the power supply, heating the substrate rack, and keeping the heating temperature at 200°C; pumping the vacuum of the reaction chamber to 1.5×10 -4 Pa; feed nitrogen and hydrogen, the flow rates are 7sccm and 3sccm respectively; adjust the working pressure of the reaction chamber to keep it at 3Pa; turn on the RF power supply, preheat for 5 minutes, set the frequency and power to 456KHz and 1200W respectively; adjust the RF matching , until the plasma is generated by the glow; continue to feed the above-mentioned nitrogen and hydrogen, and keep heating the substrate holder at 200 ° C, and start timing at the same time; after 10 minutes, turn off the radio frequency powe...
PUM
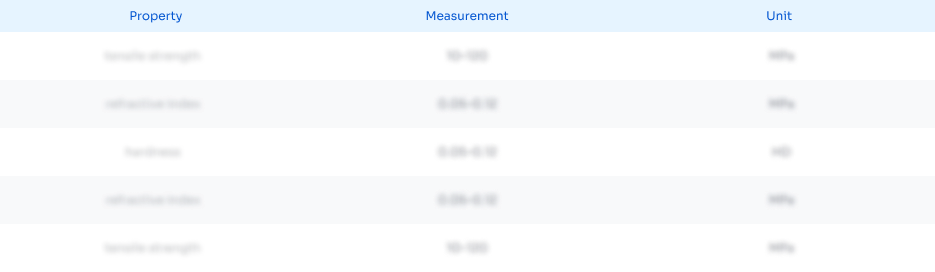
Abstract
Description
Claims
Application Information

- R&D Engineer
- R&D Manager
- IP Professional
- Industry Leading Data Capabilities
- Powerful AI technology
- Patent DNA Extraction
Browse by: Latest US Patents, China's latest patents, Technical Efficacy Thesaurus, Application Domain, Technology Topic, Popular Technical Reports.
© 2024 PatSnap. All rights reserved.Legal|Privacy policy|Modern Slavery Act Transparency Statement|Sitemap|About US| Contact US: help@patsnap.com