Laser-chemical preparation method of monocrystal silicon substrate sub-micron pyramid structure
A technology of pyramid structure and single crystal silicon, which is applied in chemical instruments and methods, single crystal growth, single crystal growth, etc., can solve the problems of high environmental requirements, achieve high controllability, simple process, ensure periodicity and uniformity effect
- Summary
- Abstract
- Description
- Claims
- Application Information
AI Technical Summary
Problems solved by technology
Method used
Image
Examples
Embodiment 1
[0023] Soak the monocrystalline silicon in acetone solution for 6 minutes; soak in HF solution with a mass fraction of 10% for 10 minutes; immerse in ethanol solution for 6 minutes, rinse and dry; A single layer of SiO with hexagonal close-packed distribution is arranged on the surface of the sheet sample 2 Place the microspheres in the air to dry naturally for 1 hour; place the monocrystalline silicon sample on the target platform, adjust the optical path so that the uniform beam spot size is larger than the sample size, and perform single-pulse irradiation. The laser is an excimer laser with a wavelength of 248nm ; Using pulse energy density 150mJ / cm 2 , with a frequency of 3 Hz; immerse the irradiated monocrystalline silicon sample in ethanol solution for 5 minutes; soak in 10% HF solution for 10 minutes to remove residual SiO 2 Microspheres: Immerse the cleaned monocrystalline silicon sample in an aqueous sodium hydroxide solution containing ethanol, corrode it for 30 sec...
Embodiment 2
[0026] Soak the monocrystalline silicon in acetone solution for 10 minutes; immerse in HF solution with a mass fraction of 15% for 6 minutes; immerse in ethanol solution for 10 minutes, rinse and dry; A single layer of SiO with hexagonal close-packed distribution is arranged on the surface of the sheet sample 2 Place the microspheres in the air to dry naturally for 1 hour; place the monocrystalline silicon sample on the target platform, adjust the optical path so that the uniform beam spot size is larger than the sample size, and perform single-pulse irradiation. The laser is an excimer laser with a wavelength of 248nm ; Using pulse energy density 400mJ / cm 2 , with a frequency of 3 Hz; immerse the irradiated monocrystalline silicon sample in ethanol solution for 5 minutes; soak in HF solution with a mass fraction of 15% for 10 minutes to remove residual SiO 2 Microspheres; immerse the cleaned monocrystalline silicon sample in an aqueous sodium hydroxide solution containing et...
Embodiment 3
[0029] Soak the monocrystalline silicon in acetone solution for 8 minutes; immerse in 5% HF solution for 8 minutes; immerse in ethanol solution and ultrasonically clean it for 8 minutes, rinse and dry; A single layer of SiO with hexagonal close-packed distribution is arranged on the surface of the sheet sample 2 Place the microspheres in the air to dry naturally for 1 hour; place the monocrystalline silicon sample on the target platform, adjust the optical path so that the uniform beam spot size is larger than the sample size, and perform single-pulse irradiation. The laser is an excimer laser with a wavelength of 248nm ; Using pulse energy density 100mJ / cm 2 , with a frequency of 3 Hz; immerse the irradiated monocrystalline silicon sample in ethanol solution for 5 minutes; immerse in HF solution with a mass fraction of 15% for 8 minutes to remove residual SiO 2Microspheres: Immerse the cleaned monocrystalline silicon sample in an aqueous solution of sodium hydroxide containi...
PUM
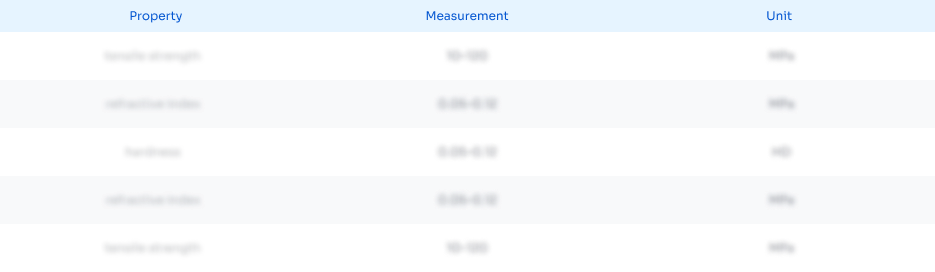
Abstract
Description
Claims
Application Information

- R&D
- Intellectual Property
- Life Sciences
- Materials
- Tech Scout
- Unparalleled Data Quality
- Higher Quality Content
- 60% Fewer Hallucinations
Browse by: Latest US Patents, China's latest patents, Technical Efficacy Thesaurus, Application Domain, Technology Topic, Popular Technical Reports.
© 2025 PatSnap. All rights reserved.Legal|Privacy policy|Modern Slavery Act Transparency Statement|Sitemap|About US| Contact US: help@patsnap.com