Composite material plate structure damage monitoring method
A technology for composite material plate and damage monitoring, which is applied in the processing of detection response signals and the use of sound waves/ultrasonic waves/infrasonic waves to analyze solids, etc. It can solve the problem that the arrival time of scattered wave packets cannot be extracted, the efficiency of damage monitoring is reduced, and damage scattering cannot be accurately extracted Wave packet arrival time and other issues, to achieve high accuracy, save time, and eliminate interference
- Summary
- Abstract
- Description
- Claims
- Application Information
AI Technical Summary
Problems solved by technology
Method used
Image
Examples
Embodiment 1
[0047] This preferred embodiment provides a damage monitoring method for a composite material plate structure based on piezoelectric elements and Lamb waves. This method uses the damage factor method to pre-judge the damage position of the composite material plate structure to be monitored, and then images the area where the damage is predicted to determine the exact position of the damage.
[0048] Because there is no need to image the non-damaged area, a lot of monitoring time is saved, and the efficiency is higher and the accuracy is higher.
[0049] Such as figure 1 As shown, the method is to fix the composite material board 12 to be monitored on the monitoring device table 11 , and fix multiple piezoelectric elements 13 on the composite material board 12 . The piezoelectric elements 13 can be arranged in various shapes, preferably, a rectangular area is surrounded by four piezoelectric elements 13 . When the area of the composite material plate 12 is large and there a...
Embodiment 2
[0087] This preferred embodiment provides a damage monitoring method for a composite material plate structure based on piezoelectric elements and Lamb waves. This method uses the damage factor method to pre-judge the damage position of the composite material plate structure to be monitored, and then images the area where the damage is predicted to determine the exact position of the damage.
[0088] The specific steps of the method are not limited, and it is only necessary to perform imaging on the area where the damage is predicted to determine the exact location of the damage; the selected damage factor and imaging method are not limited to the example given in the first preferred embodiment. Other damage factors and imaging methods are also available; when there are fewer subregions containing damage, it is not necessary to judge whether the subregion forms a fusion subregion with adjacent subregions.
[0089] Figure 12 It is the imaging diagram of this preferred embodime...
PUM
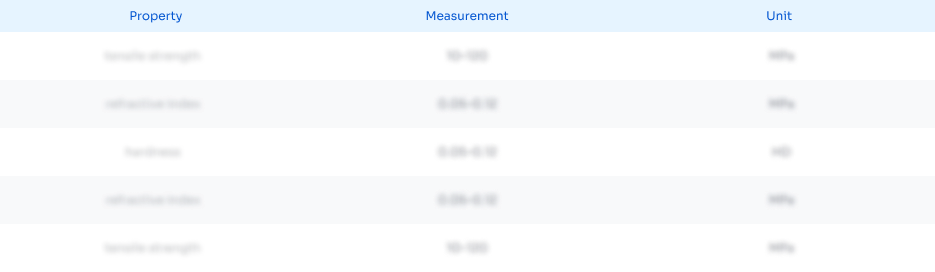
Abstract
Description
Claims
Application Information

- R&D
- Intellectual Property
- Life Sciences
- Materials
- Tech Scout
- Unparalleled Data Quality
- Higher Quality Content
- 60% Fewer Hallucinations
Browse by: Latest US Patents, China's latest patents, Technical Efficacy Thesaurus, Application Domain, Technology Topic, Popular Technical Reports.
© 2025 PatSnap. All rights reserved.Legal|Privacy policy|Modern Slavery Act Transparency Statement|Sitemap|About US| Contact US: help@patsnap.com