Method for separating and recycling vanadium and chromium from chromium vanadium reducing slag
A technology for separation and recovery of vanadium and chromium, applied in the direction of improving process efficiency, etc., can solve problems such as high roasting temperature, complicated methods, and difficult industrial production
- Summary
- Abstract
- Description
- Claims
- Application Information
AI Technical Summary
Problems solved by technology
Method used
Examples
Embodiment 1
[0041] This example is used to illustrate the method for separating and recovering vanadium and chromium from vanadium-chromium reduction slag of the present invention.
[0042] 500g of vanadium chromium reduction slag (the content of vanadium element is 5.67% by weight, the content of chromium element is 23.12% by weight) and 17g of sodium chromate are roasted at 350 ℃ for 90min (open the furnace door and feed into the air); the material after roasting Water immersion with water at a weight ratio of 1:4, the temperature of the water immersion is 80°C, the time is 2h, and then the solid-liquid separation is carried out, and the obtained liquid phase is the leach solution of vanadium, wherein the concentration of vanadium is 13.73g / L, The chromium concentration is 0.2g / L, and the vanadium leaching rate is 96.86% by weight; the obtained solid phase (477g) is carried out acid leaching for 30min at 60° C. in 1520 g of pH of 2 sulfuric acid aqueous solution, and carries out solid-li...
Embodiment 2
[0044] This example is used to illustrate the method for separating and recovering vanadium and chromium from vanadium-chromium reduction slag of the present invention.
[0045] With 500g vanadium-chromium reduction slag (the content of vanadium element is 15% by weight, the content of chromium element is 4.5% by weight) and 37.8g sodium dichromate roasting 120min at 400 ℃ (open furnace door and feed into air); The material and water are immersed in water at a weight ratio of 1:2. The temperature of the water immersion is 85° C., and the time is 4 hours. Then, solid-liquid separation is carried out. The obtained liquid phase is the leachate of vanadium, wherein the concentration of vanadium is 72.69g / L, chromium concentration 0.11g / L, vanadium leaching rate is 96.92% by weight; Gained solid phase (439g) is carried out acid leaching 30min at 90 ℃ in the aqueous hydrochloric acid solution of 0.5 with the pH of 2000g, and carries out solid-liquid separation, The obtained liquid ...
Embodiment 3
[0047] This example is used to illustrate the method for separating and recovering vanadium and chromium from vanadium-chromium reduction slag of the present invention.
[0048] With 500g vanadium-chromium reducing slag (the content of vanadium element is 1.5% by weight, the content of chromium element is 30% by weight), 4.68g sodium chromate and 5.66g sodium dichromate roasting 100min at 380 ℃ (open furnace door and pass into air); the roasted material and water are immersed in water at a weight ratio of 1:8, the temperature of the water immersion is 80° C., and the time is 3 hours, and then solid-liquid separation is carried out, and the obtained liquid phase is the leaching solution of vanadium, wherein, The vanadium concentration is 1.815g / L, the chromium concentration is 0g / L, and the vanadium leaching rate is 96.5% by weight; the obtained solid phase (496.2g) is carried out alkaline leaching at 80°C for 30min in 1620g of 3mol / L sodium hydroxide aqueous solution , and car...
PUM
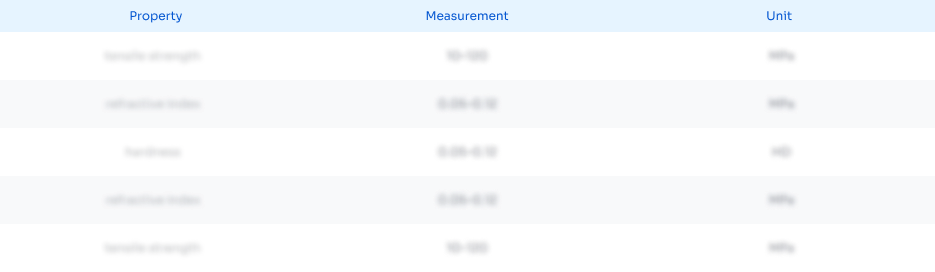
Abstract
Description
Claims
Application Information

- R&D
- Intellectual Property
- Life Sciences
- Materials
- Tech Scout
- Unparalleled Data Quality
- Higher Quality Content
- 60% Fewer Hallucinations
Browse by: Latest US Patents, China's latest patents, Technical Efficacy Thesaurus, Application Domain, Technology Topic, Popular Technical Reports.
© 2025 PatSnap. All rights reserved.Legal|Privacy policy|Modern Slavery Act Transparency Statement|Sitemap|About US| Contact US: help@patsnap.com