Positive electrode material of high-nickel lithium ion battery, preparation method of positive electrode material and lithium ion battery comprising positive electrode material
A lithium-ion battery and cathode material technology, applied in battery electrodes, secondary batteries, circuits, etc., can solve the problems of irregular structure, low energy density of materials, mixed cations of materials, etc. High density, reducing the effect of cation mixing
- Summary
- Abstract
- Description
- Claims
- Application Information
AI Technical Summary
Problems solved by technology
Method used
Image
Examples
Embodiment 1
[0047] Weigh 0.4035kg of lithium carbonate and 1kg of nickel-cobalt-aluminum precursor Ni 0.8 co 0.15 al 0.05 (OH) 2 Pour it into the mixer, load 3kg zirconia balls at the same time, and mix at a speed of 7r / min for 5 hours; after mixing evenly, weigh 0.146kg of sodium peroxide and quickly mix it in, and continue to mix in the mixer at a speed of 7r / min for 0.5 h; After mixing evenly, take out the zirconia balls and sinter at a high temperature of 700°C, during which air is introduced at 6L / h. After sintering for 20 hours, the material is cooled to room temperature, and crushed through a 200-mesh sieve to obtain 1.02kg of lithium nickel cobalt aluminate; Pour the nickel-cobalt-lithium-aluminate powder into 3L of water and stir at room temperature for 3 hours, then centrifuge at 2000rpm for 40 minutes, remove the upper solution, and dry the solid slurry at 120°C for 15 hours to obtain the positive electrode material nickel-cobalt lithium aluminate LiNi 0.8 co 0.15 al 0.05 ...
Embodiment 2
[0049] Weigh 0.1658kg lithium hydroxide and 1kg nickel cobalt manganese precursor Ni 0.90 co 0.05 mn 0.05 C 2 o 4 Pour it into the mixer, load 4kg polyurethane balls at the same time, and mix at a speed of 15r / min for 10h; after mixing evenly, weigh 0.287kg of the mixture of sodium peroxide and rubidium peroxide and mix it quickly, and continue to mix it in the mixer at 10r / min. Mix at a speed of min for 1 hour; after mixing evenly, take out the polyurethane balls and sinter at a high temperature of 850°C, during which oxygen is introduced at 4L / h. After sintering for 20 hours, the material is cooled to room temperature and crushed through a 200-mesh sieve to obtain 1.13kg of nickel-cobalt manganese acid Lithium: Pour nickel-cobalt lithium manganate powder into 5L water and stir at room temperature for 2 hours, then centrifuge at 2500rpm for 30 minutes, remove the upper solution, and dry the solid slurry at 200°C for 10 hours to obtain the positive electrode material lithiu...
Embodiment 3
[0051] Weigh 0.5507kg of lithium acetate and 1kg of nickel-cobalt-manganese precursor Ni 0.70 co 0.15 mn 0.15 CO 3 Pour into a mixer and mix for 8 hours at a speed of 10r / min; after mixing evenly, weigh 0.225kg of a mixture of sodium peroxide and potassium peroxide and quickly mix it into it, and continue mixing in the mixer for 0.5h at a speed of 10r / min; mix After uniformity, it was sintered at a high temperature of 650°C, and air was introduced at 6L / h during the period. After sintering for 30 hours, the material was cooled to room temperature and crushed through a 200-mesh sieve to obtain 1.03kg nickel-cobalt lithium manganese oxide; pour the nickel-cobalt lithium manganese oxide powder Put into 5L of water and stir at room temperature for 2h, then centrifuge at 3000rpm for 25min, remove the upper layer solution, and dry the solid slurry at 300°C for 6h to obtain the positive electrode material nickel cobalt lithium manganate LiNi 0.70 co 0.15 mn 0.15 o 2 .
PUM
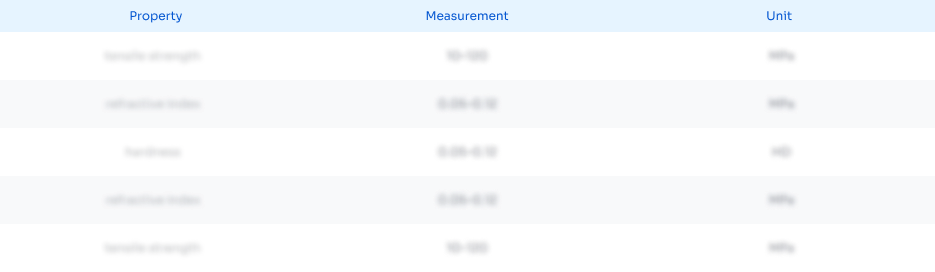
Abstract
Description
Claims
Application Information

- R&D
- Intellectual Property
- Life Sciences
- Materials
- Tech Scout
- Unparalleled Data Quality
- Higher Quality Content
- 60% Fewer Hallucinations
Browse by: Latest US Patents, China's latest patents, Technical Efficacy Thesaurus, Application Domain, Technology Topic, Popular Technical Reports.
© 2025 PatSnap. All rights reserved.Legal|Privacy policy|Modern Slavery Act Transparency Statement|Sitemap|About US| Contact US: help@patsnap.com