Rolling bearing failure diagnosis method base on vibration temporal frequency analysis
A rolling bearing and fault diagnosis technology, which is applied in mechanical bearing testing and other directions, can solve the problems of complex vibration signals, increased calculation amount, and limited fault diagnosis accuracy, etc., and achieve the effect of fast and accurate identification
- Summary
- Abstract
- Description
- Claims
- Application Information
AI Technical Summary
Problems solved by technology
Method used
Image
Examples
Embodiment Construction
[0027] A detailed description of the rolling bearing fault diagnosis method based on vibration time-frequency analysis of the present invention will be given below in conjunction with embodiments and drawings.
[0028] The invention provides a rolling bearing fault diagnosis method based on vibration time-frequency analysis, such as figure 1 As shown, including the following steps:
[0029] (1) Use the vibration acceleration sensor to collect the vibration signals of the rolling bearing under normal and fault conditions;
[0030] (2) Improve the interpolation method and end effect processing method in the intrinsic time scale decomposition, and use the improved intrinsic time scale decomposition method to decompose the collected vibration signal x(t) to generate several intrinsic time scales Component HF m (t) and residual signal u n (t):
[0031] x ( t ) = X m = 1 n HF m ( t ) + u n ( t ) ;
[0032] Wherein, the interpolati...
PUM
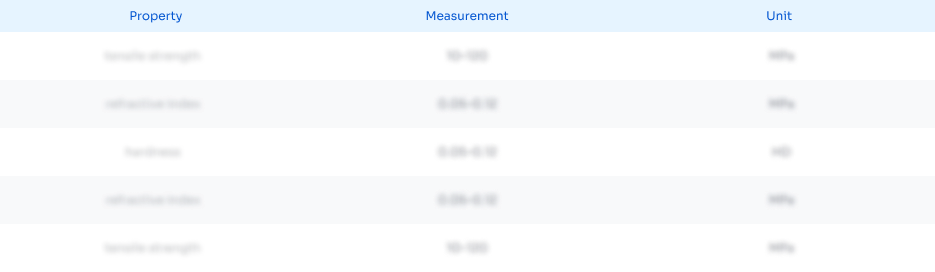
Abstract
Description
Claims
Application Information

- Generate Ideas
- Intellectual Property
- Life Sciences
- Materials
- Tech Scout
- Unparalleled Data Quality
- Higher Quality Content
- 60% Fewer Hallucinations
Browse by: Latest US Patents, China's latest patents, Technical Efficacy Thesaurus, Application Domain, Technology Topic, Popular Technical Reports.
© 2025 PatSnap. All rights reserved.Legal|Privacy policy|Modern Slavery Act Transparency Statement|Sitemap|About US| Contact US: help@patsnap.com