High-intensity high-toughness Mg-Zn-Y-Gd-Zr alloy and preparation method thereof
A high-toughness, high-strength technology, applied in the field of alloys and their preparation, can solve the problems of high rare earth content in alloys
- Summary
- Abstract
- Description
- Claims
- Application Information
AI Technical Summary
Problems solved by technology
Method used
Image
Examples
specific Embodiment approach 1
[0021] Specific Embodiment 1: In this embodiment, the high-strength and high-toughness Mg-Zn-Y-Gd-Zr alloy consists of 8-12% Zn, 1-6% Y, 1-6% Gd, 0.3-0.7% Zr and The balance is composed of Mg.
specific Embodiment approach 2
[0022] Specific embodiment two: the difference between this embodiment and specific embodiment one is that the high-strength and high-toughness Mg-Zn-Y-Gd-Zr alloy consists of 8.12% Zn, 5.95% Y, 1.01% Gd, 0.31% Zr and The balance is composed of Mg. Others are the same as in the first embodiment.
specific Embodiment approach 3
[0023] Specific embodiment three: The difference between this embodiment and specific embodiment one or two is that the high-strength and high-toughness Mg-Zn-Y-Gd-Zr alloy consists of 10.06% Zn, 4.75% Y, 1.32% Gd, Composition of 0.46% Zr and balance Mg. Others are the same as those in the first or second embodiment.
PUM
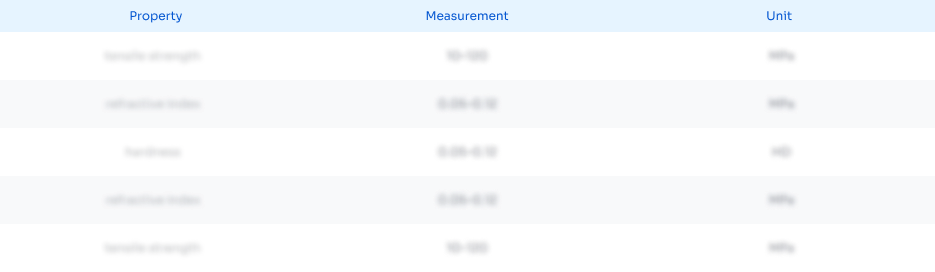
Abstract
Description
Claims
Application Information

- R&D Engineer
- R&D Manager
- IP Professional
- Industry Leading Data Capabilities
- Powerful AI technology
- Patent DNA Extraction
Browse by: Latest US Patents, China's latest patents, Technical Efficacy Thesaurus, Application Domain, Technology Topic, Popular Technical Reports.
© 2024 PatSnap. All rights reserved.Legal|Privacy policy|Modern Slavery Act Transparency Statement|Sitemap|About US| Contact US: help@patsnap.com