Method for reducing alkali metal enrichment in blast furnace
A technology of alkali metals and alkali metal oxides, applied in blast furnaces, blast furnace details, furnaces, etc., can solve problems such as strength reduction, pulverization, and furnace wall nodules, and achieve improved fluidity, increased alkali removal rate, and protection of furnace linings Effect
- Summary
- Abstract
- Description
- Claims
- Application Information
AI Technical Summary
Problems solved by technology
Method used
Image
Examples
Embodiment Construction
[0012] The technical solutions of the present invention will be described in detail below in conjunction with the accompanying drawings and embodiments.
[0013] In January 2014, when the load of alkali metal oxides into the furnace was 2.75kg / t, the blast furnace discharged alkali for 18 days.
[0014] During the alkali discharge period, the MgO content in the blast furnace slag is controlled to be between 7.45% and 8.35%, and the binary basicity of the slag is not greater than 1.15; 0.31-0.58%; the Ti content of blast furnace molten iron is controlled at 0.1%-0.15%.
[0015] According to the division of the three stages before alkali discharge, during alkali discharge and after alkali discharge, the raw fuel furnace, slag and dust were sampled successively. The slag composition and alkali balance calculation results are shown in Table 1. The alkali in the table Both load and alkali discharge rate refer to K 2 O and Na 2 The sum of O.
[0016] Table 1: Slag composition an...
PUM
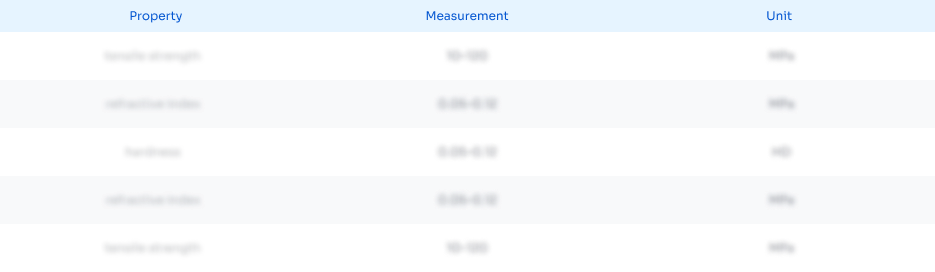
Abstract
Description
Claims
Application Information

- R&D Engineer
- R&D Manager
- IP Professional
- Industry Leading Data Capabilities
- Powerful AI technology
- Patent DNA Extraction
Browse by: Latest US Patents, China's latest patents, Technical Efficacy Thesaurus, Application Domain, Technology Topic, Popular Technical Reports.
© 2024 PatSnap. All rights reserved.Legal|Privacy policy|Modern Slavery Act Transparency Statement|Sitemap|About US| Contact US: help@patsnap.com