Method for flexible design of spiral groove skew rolling roller
A design method and technology of spiral holes, applied in the direction of rolls, metal rolling, metal rolling, etc., can solve the problems of reduced design accuracy, complicated design process, cumbersome and complicated, etc., to avoid errors, accurate three-dimensional design, and ensure design accuracy Effect
- Summary
- Abstract
- Description
- Claims
- Application Information
AI Technical Summary
Problems solved by technology
Method used
Image
Examples
example 1
[0074] In the following, the establishment and reliability of the parameter model of the roll for cross-rolling of spherical parts will be discussed by taking the roll for cross-rolling of bearing steel balls with a radius R of 15 mm as an example.
[0075] 1) According to the cross-rolling process design method, calculate the parameters of the roll pass for the cross-rolling forming of bearing steel balls with a radius R of 15mm, and input each parameter into the parameter list of the parametric model as shown below (the unit of length is mm , angles are in degrees).
[0076]
[0077]
[0078] 2) Take the base circle of the roll as the cross-section profile, and create a cylindrical solid feature through the stretch command. The cross-sectional circular size is determined by the diameter D in the parameter list b = 150mm driving to get.
[0079] 3) Create the initial rib helical trajectory and profile section, and create the initial helical rib on the solid cylindrica...
PUM
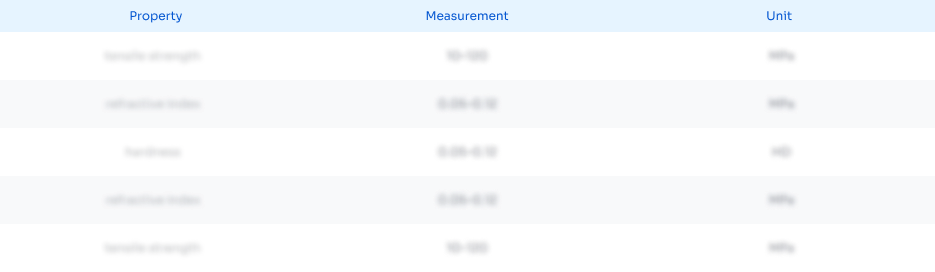
Abstract
Description
Claims
Application Information

- R&D
- Intellectual Property
- Life Sciences
- Materials
- Tech Scout
- Unparalleled Data Quality
- Higher Quality Content
- 60% Fewer Hallucinations
Browse by: Latest US Patents, China's latest patents, Technical Efficacy Thesaurus, Application Domain, Technology Topic, Popular Technical Reports.
© 2025 PatSnap. All rights reserved.Legal|Privacy policy|Modern Slavery Act Transparency Statement|Sitemap|About US| Contact US: help@patsnap.com