Catalyst for producing low-carbon olefin by using synthesis gas and preparation method of catalyst
A technology of low-carbon olefins and catalysts, applied in the field of catalysts and their preparation, can solve the problems of low selectivity of low-carbon olefins, low CO conversion rate, etc., and achieve the effects of increasing conversion rate, increasing selectivity, and enhancing interaction strength
- Summary
- Abstract
- Description
- Claims
- Application Information
AI Technical Summary
Problems solved by technology
Method used
Examples
Embodiment 1
[0032] Mix 60.0g α-alumina and 40.0g ZSM-5 molecular sieve (silicon-aluminum ratio 100) powder evenly, press tablet and sieve into 60-80 mesh to prepare composite carrier H; 134.9g ferric nitrate nonahydrate, 35.6g 50% Manganese nitrate solution, 14.5g lanthanum nitrate hexahydrate, and 1.7g potassium nitrate were dissolved in 35.0g water to make mixed solution I; under the condition of vacuum degree of 80kPa, the above mixed solution I was impregnated in 60.0 g prepared Catalyst precursor J was obtained on the composite carrier H; the impregnated catalyst precursor J was dried at 110°C, and then calcined at 450°C for 2 hours to obtain a catalyst for producing low-carbon olefins from syngas. The weight of the active component and the composite carrier in the catalyst is 40% and 60% respectively, the weight ratio of ZSM-5 molecular sieve and α-alumina in the composite carrier, and the general composition formula of the atomic ratio of the active component is as follows:
[0033...
Embodiment 2
[0037] Mix 99.0g of α-alumina and 1.0g of ZSM-5 molecular sieve (silicon-aluminum ratio 100) powder evenly, press and sieve into 60-80 mesh to prepare composite carrier H; 134.9g of ferric nitrate nonahydrate, 35.6g of 50% Manganese nitrate solution, 14.5g lanthanum nitrate hexahydrate, and 1.7g potassium nitrate were dissolved in 35.0g water to make mixed solution I; under the condition of vacuum degree of 80kPa, the above mixed solution I was impregnated in 60.0 g prepared Catalyst precursor J was obtained on the composite carrier H; the impregnated catalyst precursor J was dried at 110°C, and then calcined at 450°C for 2 hours to obtain a catalyst for producing low-carbon olefins from syngas. The weight of the active component and the composite carrier in the catalyst is 40% and 60% respectively, the weight ratio of ZSM-5 molecular sieve and α-alumina in the composite carrier, and the general composition formula of the atomic ratio of the active component is as follows:
[...
Embodiment 3
[0042] Mix 20.0g α-alumina and 80.0g ZSM-5 molecular sieve (silicon-alumina ratio 100) powder evenly, press tablet and sieve into 60-80 mesh to prepare composite carrier H; 134.9g ferric nitrate nonahydrate, 35.6g 50% Manganese nitrate solution, 14.5g lanthanum nitrate hexahydrate, and 1.7g potassium nitrate were dissolved in 35.0g water to make mixed solution I; under the condition of vacuum degree of 80kPa, the above mixed solution I was impregnated in 60.0 g prepared Catalyst precursor J was obtained on the composite carrier H; the impregnated catalyst precursor J was dried at 110°C, and then calcined at 450°C for 2 hours to obtain a catalyst for producing low-carbon olefins from syngas. The weight of the active component and the composite carrier in the catalyst is 40% and 60% respectively, the weight ratio of ZSM-5 molecular sieve and α-alumina in the composite carrier, and the general composition formula of the atomic ratio of the active component is as follows:
[0043]...
PUM
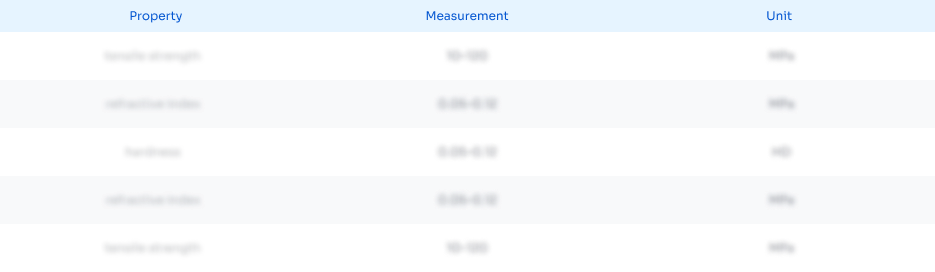
Abstract
Description
Claims
Application Information

- R&D Engineer
- R&D Manager
- IP Professional
- Industry Leading Data Capabilities
- Powerful AI technology
- Patent DNA Extraction
Browse by: Latest US Patents, China's latest patents, Technical Efficacy Thesaurus, Application Domain, Technology Topic, Popular Technical Reports.
© 2024 PatSnap. All rights reserved.Legal|Privacy policy|Modern Slavery Act Transparency Statement|Sitemap|About US| Contact US: help@patsnap.com