A worm and worm gear decelerating mechanism
A worm gear reduction, worm gear technology, applied in the direction of gear vibration/noise attenuation, mechanical equipment, gear transmission, etc., can solve the problems of small torque, small speed reduction, and large noise of the reduction mechanism, so as to reduce the speed and reduce the impact force, increased torque, and reduction ratio effects
- Summary
- Abstract
- Description
- Claims
- Application Information
AI Technical Summary
Problems solved by technology
Method used
Image
Examples
Embodiment 1
[0036] A worm gear reduction mechanism, such as figure 1 As shown, it includes a drive mechanism 1, a first worm gear transmission mechanism 2 connected to the drive mechanism 1, and a second worm gear transmission mechanism 3. The first worm gear transmission mechanism 2 includes a first drive worm 201, which is connected to the first worm gear 201 respectively. The first worm gear 202 and the second worm gear 203 meshed by the first drive worm 201, one end of the first drive worm 201 is drivingly connected with the drive mechanism 1, and the second worm gear transmission mechanism 3 includes a first drive worm 301, a second worm gear 301 Two transmission worms 302 and the third worm gear 303 meshing with the first transmission worm 301 and the second transmission worm 302 respectively, the first worm gear 202 is drivingly connected with the first transmission worm 301, and the second The turbine 203 is drivingly connected with the second transmission worm 302 , and the third...
Embodiment 2
[0045] A kind of worm gear reduction mechanism of the present invention, such as figure 2 As shown, the main technical solutions of this embodiment are basically the same as those of Embodiment 1, and the features not explained in this embodiment are explained in Embodiment 1, and will not be repeated here. The difference between this embodiment and embodiment 1 is:
[0046] The output mechanism 4 is set as a horizontal output mechanism 4, and the horizontal output mechanism 4 is provided with an output main shaft, and one end of the output main shaft is connected with the third turbine 303 through a bearing; the driving mechanism 1 is provided with a driving motor 101, the The motor shaft of the driving motor 101 is drivingly connected with the first driving worm 201 through a bearing.
[0047] Through the horizontal output mechanism, the driving force of the driving mechanism 1 through the first worm gear transmission mechanism 2 and the second worm gear transmission mecha...
PUM
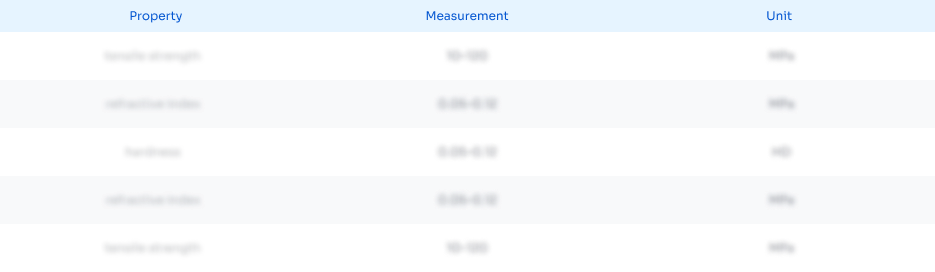
Abstract
Description
Claims
Application Information

- R&D
- Intellectual Property
- Life Sciences
- Materials
- Tech Scout
- Unparalleled Data Quality
- Higher Quality Content
- 60% Fewer Hallucinations
Browse by: Latest US Patents, China's latest patents, Technical Efficacy Thesaurus, Application Domain, Technology Topic, Popular Technical Reports.
© 2025 PatSnap. All rights reserved.Legal|Privacy policy|Modern Slavery Act Transparency Statement|Sitemap|About US| Contact US: help@patsnap.com