Fluid pipeline leak detection and positioning method
A technology of leak detection and positioning method, which is applied in the direction of fluid tightness test, pipeline system, measuring device, etc., and can solve problems such as large amount of calculation, increased problem complexity, and decreased positioning accuracy
- Summary
- Abstract
- Description
- Claims
- Application Information
AI Technical Summary
Problems solved by technology
Method used
Image
Examples
Embodiment Construction
[0069] A method for detecting and locating fluid pipeline leaks, including a pipeline under test. The innovation is that at least two sensing devices are arranged on the pipeline under test, and there is a certain distance between the two sensing devices. collection point, the sensing device can simultaneously sense pipeline acoustic vibrations in two directions, the two directions being the pipeline axial direction and the pipeline radial direction; when there is leakage on the measured pipeline between the two collection points When the leak point is detected, locate the leak point according to the following methods:
[0070] Let the two collection points be collection point 1 and collection point 2 respectively, the distance between the two collection points is denoted as L, and the distance between collection point 1 and the leakage point is denoted as l 1 , the distance between collection point 2 and leakage point is denoted as l 2 , the propagation velocity of the longi...
PUM
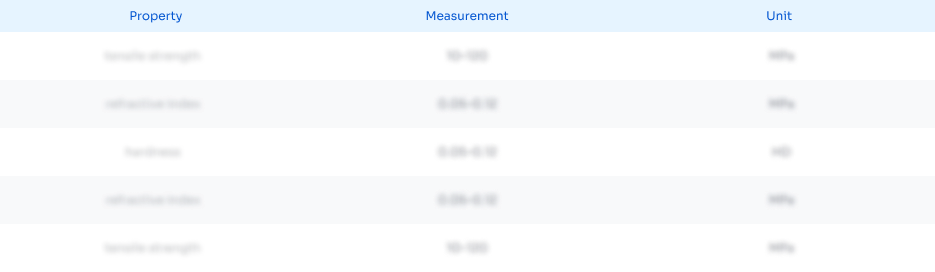
Abstract
Description
Claims
Application Information

- R&D Engineer
- R&D Manager
- IP Professional
- Industry Leading Data Capabilities
- Powerful AI technology
- Patent DNA Extraction
Browse by: Latest US Patents, China's latest patents, Technical Efficacy Thesaurus, Application Domain, Technology Topic, Popular Technical Reports.
© 2024 PatSnap. All rights reserved.Legal|Privacy policy|Modern Slavery Act Transparency Statement|Sitemap|About US| Contact US: help@patsnap.com