A synchronous online monitoring device for low-temperature corrosion process and state of flue gas cooler
A flue gas cooler, low-temperature corrosion technology, used in measuring devices, weather resistance/light resistance/corrosion resistance, instruments, etc., can solve the problem of off-line detection of flue gas coolers that cannot be known, do not have one, and cannot be regularly cut off, etc. problem, to achieve the effect of convenient results, simple structure, and coal saving
- Summary
- Abstract
- Description
- Claims
- Application Information
AI Technical Summary
Problems solved by technology
Method used
Image
Examples
Embodiment
[0033] The constant wall temperature heat exchange tube 3 is filled with working medium water for heat exchange, or other working medium whose boiling point is within the working temperature range of the heat exchanger is used. When the inner pressure of the constant wall temperature heat exchange tube 3 is determined, its internal The saturation temperature of the working medium is also uniquely determined, thereby ensuring the stability of the tube wall temperature of the constant wall temperature heat exchange tube 3; the blower 7 sends the high-speed airflow through the air pipeline 6 into the forced heat dissipation casing 4, and passes through the regulating valve. 5. Adjust the air flow; the condensing section of the constant wall temperature heat exchange tube 3 exchanges heat with the air introduced into the casing 4.
[0034] like figure 1 and Figure 4 As shown in the figure, the working principle of the present invention is as follows: in the flow direction of the...
PUM
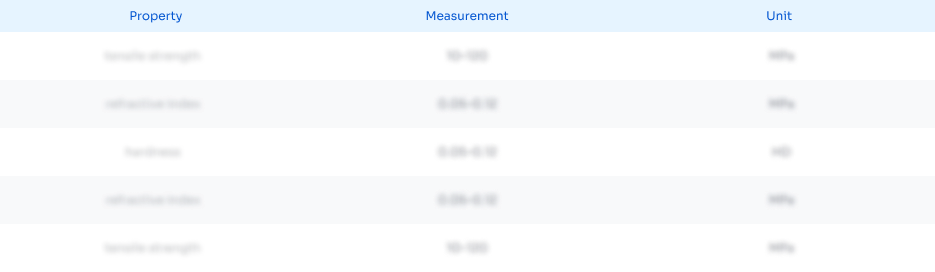
Abstract
Description
Claims
Application Information

- Generate Ideas
- Intellectual Property
- Life Sciences
- Materials
- Tech Scout
- Unparalleled Data Quality
- Higher Quality Content
- 60% Fewer Hallucinations
Browse by: Latest US Patents, China's latest patents, Technical Efficacy Thesaurus, Application Domain, Technology Topic, Popular Technical Reports.
© 2025 PatSnap. All rights reserved.Legal|Privacy policy|Modern Slavery Act Transparency Statement|Sitemap|About US| Contact US: help@patsnap.com