Method for directly smelting copper-bearing antibacterial stainless steel by utilizing copper slag for reducing molten iron
An antibacterial stainless steel and copper slag technology, applied in the field of metallurgy, can solve the problems of high cost, no consideration of the removal of harmful components, and high smelting temperature, and achieves the effect of reducing production costs, improving the added value of comprehensive utilization, and wide adaptability
- Summary
- Abstract
- Description
- Claims
- Application Information
AI Technical Summary
Problems solved by technology
Method used
Image
Examples
Embodiment 1
[0061] A method for directly smelting copper-containing antibacterial stainless steel by using copper slag to reduce molten iron, the specific steps are as follows:
[0062] (1) Oxidation and impurity removal pretreatment:
[0063] The high-temperature molten copper slag at 1250°C is directly transferred into the high-temperature reduction furnace to form a molten pool with a depth of 20cm. The spray gun is inserted to a depth of 18cm. Oxygen is injected to oxidize and remove impurities from the molten copper slag. Eccentric mechanical stirring, injection oxygen flow rate of 400ml / min, injection pressure of 1.5MPa, injection time of 20min, stirring speed of eccentric mechanical agitation of 50rpm, to obtain sulfur content of less than 0.2mass% after oxidation and impurity removal pretreatment Molten copper slag;
[0064] (2) Smelting reduction of copper slag after pretreatment:
[0065] Add the slagging agent CaO to the molten copper slag after the pretreatment of oxidation ...
Embodiment 2
[0074] A method for directly smelting copper-containing antibacterial stainless steel by using copper slag to reduce molten iron, the specific steps are as follows:
[0075] (1) Oxidation and impurity removal pretreatment:
[0076]The high-temperature molten copper slag at 1300°C is directly transferred into the high-temperature reduction furnace to form a molten pool with a depth of 20cm. The spray gun is inserted to a depth of 18cm. Oxygen is injected to oxidize and remove impurities from the molten copper slag. Eccentric mechanical stirring, blowing oxygen flow rate of 500ml / min, blowing pressure of 1.0MPa, blowing time of 25min, stirring speed of eccentric mechanical stirring of 75rpm, to obtain sulfur content of less than 0.2mass% after oxidation and impurity removal pretreatment Molten copper slag;
[0077] (2) Smelting reduction of copper slag after pretreatment:
[0078] Add the slagging agent CaO to the molten copper slag after the pretreatment of oxidation and impu...
Embodiment 3
[0087] A method for directly smelting copper-containing antibacterial stainless steel by using copper slag to reduce molten iron, the specific steps are as follows:
[0088] (1) Oxidation and impurity removal pretreatment:
[0089] The high-temperature molten copper slag at 1350°C is directly transferred into the high-temperature reduction furnace to form a molten pool with a depth of 20cm. The spray gun is inserted to a depth of 18cm. Oxygen is injected to oxidize and remove impurities from the molten copper slag. Eccentric mechanical stirring, injection oxygen flow rate is 600ml / min, injection pressure is 0.5MPa, injection time is 30min, and the stirring speed of eccentric mechanical agitation is 100rpm, and the sulfur content is lower than 0.2mass%. molten copper slag;
[0090] (2) Smelting reduction of copper slag after pretreatment:
[0091] Add the slagging agent CaO to the molten copper slag after the pretreatment of oxidation and impurity removal, adjust the basicity...
PUM
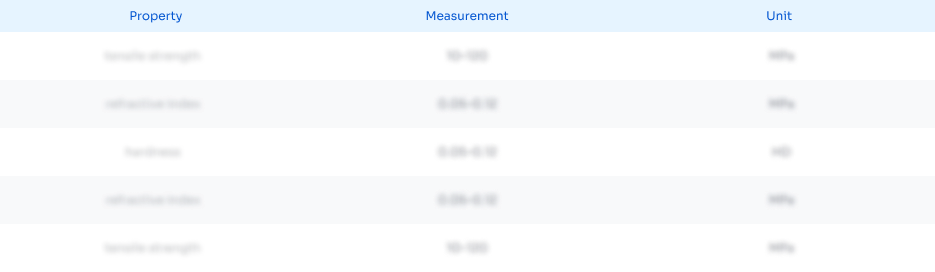
Abstract
Description
Claims
Application Information

- R&D
- Intellectual Property
- Life Sciences
- Materials
- Tech Scout
- Unparalleled Data Quality
- Higher Quality Content
- 60% Fewer Hallucinations
Browse by: Latest US Patents, China's latest patents, Technical Efficacy Thesaurus, Application Domain, Technology Topic, Popular Technical Reports.
© 2025 PatSnap. All rights reserved.Legal|Privacy policy|Modern Slavery Act Transparency Statement|Sitemap|About US| Contact US: help@patsnap.com