Preparation method of macromolecule packaging material
A packaging material and polymer technology, applied in the field of preparation of polymer packaging materials, can solve the problems of poor cooking resistance, reduced stability of polymer packaging materials, poor barrier properties of polymer packaging materials, etc. Effects of retort resistance properties
- Summary
- Abstract
- Description
- Claims
- Application Information
AI Technical Summary
Problems solved by technology
Method used
Examples
Embodiment 1
[0024] (1) Open the reactor, set the temperature of the reactor to 155°C, add 22kg of alkyd resin, 9kg of polychloroprene, and 8kg of polycarbonate into the reactor after the temperature stabilizes, and add alkyd resin, Heat and mix polychloroprene and polycarbonate three polymer materials, mix until uniform, and keep the temperature constant for 2 hours; (2) After the heat preservation is completed, raise the temperature of the reactor to 175°C, and then add Cycloheptene is 3kg, cellulose acetate butyrate is 7kg, ethylene glycol is 9kg, silicon dioxide is 3kg, butyl rubber is 8kg, add cycloheptene, cellulose acetate butyrate, ethylene glycol, di After oxidizing silicon and butyl rubber, mix it with the mixture prepared in step (1) again until all the ingredients are evenly dispersed to form a uniform mixed packaging material; (3) After obtaining a uniform mixed packaging material, the mixed packaging The material is extruded, and the extrusion temperature is divided into four...
Embodiment 2
[0027] (1) Open the reactor, set the temperature of the reactor to 145°C, add 19kg of alkyd resin, 11kg of polychloroprene, and 12kg of polycarbonate into the reactor after the temperature stabilizes, and add alkyd resin, Heat and mix polychloroprene and polycarbonate three polymer materials, mix until uniform, and keep the temperature constant for 2 hours; (2) After the heat preservation is completed, raise the temperature of the reactor to 175°C, and then add Cycloheptene is 4kg, cellulose acetate butyrate is 8kg, ethylene glycol is 4kg, silicon dioxide is 5kg, butyl rubber is 13kg, add cycloheptene, cellulose acetate butyrate, ethylene glycol, di After oxidizing silicon and butyl rubber, mix it with the mixture prepared in step (1) again until all the ingredients are evenly dispersed to form a uniform mixed packaging material; (3) After obtaining a uniform mixed packaging material, the mixed packaging The material is extruded, and the extrusion temperature is divided into f...
Embodiment 3
[0030] (1) Open the reactor, set the temperature of the reactor to 150°C, add 21kg of alkyd resin, 13kg of polychloroprene, and 10kg of polycarbonate into the reactor after the temperature stabilizes, and add alkyd resin, Heat and mix polychloroprene and polycarbonate three polymer materials, mix until uniform, and keep the temperature constant for 2 hours; (2) After the heat preservation is completed, raise the temperature of the reactor to 175°C, and then add Cycloheptene is 6kg, cellulose acetate butyrate is 6kg, ethylene glycol is 7kg, silicon dioxide is 5kg, butyl rubber is 8kg, add cycloheptene, cellulose acetate butyrate, ethylene glycol, di After oxidizing silicon and butyl rubber, mix it with the mixture prepared in step (1) again until all the ingredients are evenly dispersed to form a uniform mixed packaging material; (3) After obtaining a uniform mixed packaging material, the mixed packaging The material is extruded, and the extrusion temperature is divided into fo...
PUM
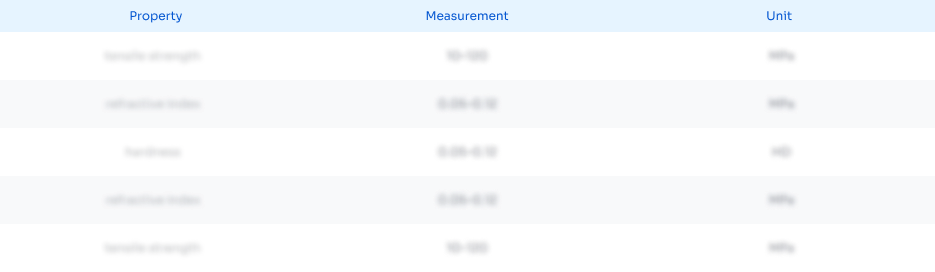
Abstract
Description
Claims
Application Information

- R&D Engineer
- R&D Manager
- IP Professional
- Industry Leading Data Capabilities
- Powerful AI technology
- Patent DNA Extraction
Browse by: Latest US Patents, China's latest patents, Technical Efficacy Thesaurus, Application Domain, Technology Topic, Popular Technical Reports.
© 2024 PatSnap. All rights reserved.Legal|Privacy policy|Modern Slavery Act Transparency Statement|Sitemap|About US| Contact US: help@patsnap.com