Preparation method of polyester for making high modulus and low shrinkage type industrial yarns
A low-shrinkage, industrial yarn technology, applied in the field of polyester manufacturing, can solve the problem that polyester cannot meet the application requirements of high-modulus and low-shrinkage industrial yarns, and achieves improved yield and performance, good purity, and good spinnability. sexual effect
- Summary
- Abstract
- Description
- Claims
- Application Information
AI Technical Summary
Problems solved by technology
Method used
Image
Examples
Embodiment 1~8
[0017] The esterification reaction of terephthalic acid and ethylene glycol is carried out at a temperature of 250-290 °C, and the molar ratio of raw materials is terephthalic acid:ethylene glycol=1:(1.1-1.5). The intermediate bishydroxyethyl terephthalate is generated, and the reaction is carried out until the esterification rate is at least 92%, and the generated water is removed during the reaction.
[0018] The intermediate bishydroxyethyl terephthalate is subjected to a polycondensation reaction under the condition of negative pressure (2000-100Pa) in the presence of a mixed catalyst system to obtain a polyester product. The polycondensation reaction temperature is 270-300°C, and the reaction time is 2 ~3 hours.
[0019] After the selected mixed catalyst enters the modulation area, ethylene glycol (hereinafter referred to as: EG) is added to dilute the catalyst concentration to 2wt%.
[0020] The control of the mixed catalyst system used in the polycondensation reaction ...
PUM
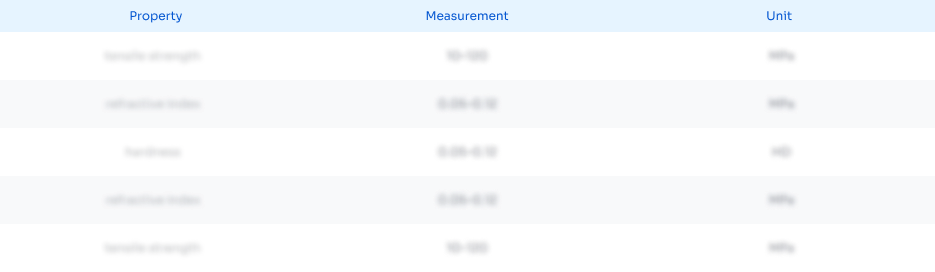
Abstract
Description
Claims
Application Information

- R&D
- Intellectual Property
- Life Sciences
- Materials
- Tech Scout
- Unparalleled Data Quality
- Higher Quality Content
- 60% Fewer Hallucinations
Browse by: Latest US Patents, China's latest patents, Technical Efficacy Thesaurus, Application Domain, Technology Topic, Popular Technical Reports.
© 2025 PatSnap. All rights reserved.Legal|Privacy policy|Modern Slavery Act Transparency Statement|Sitemap|About US| Contact US: help@patsnap.com