Reballing method for inverted packaging of semiconductor integrated circuit or discrete device
A technology of integrated circuits and discrete devices, which is applied in the field of bump packaging of semiconductor integrated circuits or discrete devices, which can solve the problems of poor heat dissipation and large parasitic effects, and achieve simple process, small parasitic parameters and low curing temperature Effect
- Summary
- Abstract
- Description
- Claims
- Application Information
AI Technical Summary
Problems solved by technology
Method used
Examples
Embodiment 1
[0016] 1) Bump bottom metallization
[0017] Sputter or evaporate titanium, nickel, and silver three layers of metal in sequence on the chip completed by pressure point lithography. The thicknesses of titanium, nickel, and silver are 1800mm respectively. 、3600 、4500 , the composite metal layer is used to connect the wiring metal and the solder ball in the chip, and then use photolithography to etch the composite metal layer in the area other than the pressure point on the chip, and retain the composite metal layer on the pressure point.
[0018] 2) Apply a layer of tin flux with a thickness of 48 microns on the chip.
[0019] 3) Place a solder ball with a diameter of 290 microns on the composite metal layer of the chip coated with tin flux, heat the chip to 220°C, solder the solder ball to the composite metal on the chip through the flux, and the metal wire inside the chip The composite metal layer on the pressure point is bonded to the solder ball bump, and finally the ...
Embodiment 2
[0021] 1) Bump bottom metallization
[0022] On the chips completed by pressure point lithography, three layers of metals, titanium, nickel, and silver are sputtered or evaporated in sequence, and the thicknesses of titanium, nickel, and silver are 1860mm respectively. 、3980 、5340 . The composite metal layer is used to connect the wiring metal and the solder balls in the chip, and then the composite metal layer in the area other than the pressure point on the chip is etched by photolithography, and the composite metal layer on the pressure point is retained.
[0023] 2) Apply a layer of tin flux with a thickness of 56 microns on the chip.
[0024] 3) Place a tin ball with a diameter of 300 microns on the chip composite metal layer coated with tin flux, heat the chip to 240°C, solder the solder ball to the composite metal on the chip through the flux, and the metal wire inside the chip The composite metal layer on the pressure point is bonded to the solder ball bump, an...
Embodiment 3
[0026] 1) Bump bottom metallization
[0027] On the chips completed by pressure point lithography, three layers of metals including titanium, nickel and silver are sputtered or evaporated sequentially. The thicknesses of titanium, nickel and silver are respectively 2200mm. , 4400 、5500 . The composite metal layer is used to connect the wiring metal and the solder balls in the chip, and then the composite metal layer in the area other than the pressure point on the chip is etched by photolithography, and the composite metal layer on the pressure point is retained.
[0028] 2) Apply a layer of tin flux with a thickness of 50 microns on the chip.
[0029] 3) Place a tin ball with a diameter of 295 microns on the composite metal layer of the chip coated with tin flux, heat the chip to 230°C, solder the solder ball to the composite metal on the chip through the flux, and the metal wire inside the chip The composite metal layer on the pressure point is bonded to the solder ba...
PUM
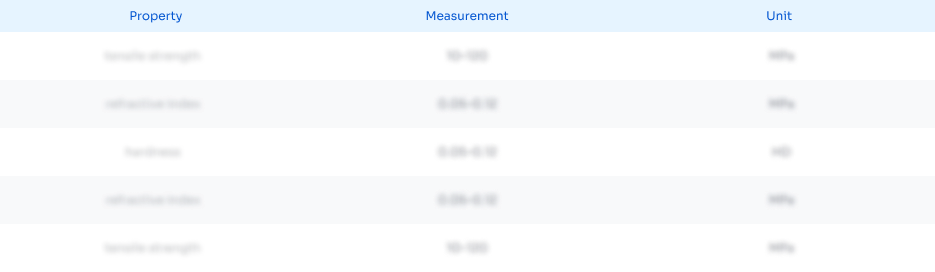
Abstract
Description
Claims
Application Information

- R&D
- Intellectual Property
- Life Sciences
- Materials
- Tech Scout
- Unparalleled Data Quality
- Higher Quality Content
- 60% Fewer Hallucinations
Browse by: Latest US Patents, China's latest patents, Technical Efficacy Thesaurus, Application Domain, Technology Topic, Popular Technical Reports.
© 2025 PatSnap. All rights reserved.Legal|Privacy policy|Modern Slavery Act Transparency Statement|Sitemap|About US| Contact US: help@patsnap.com