Aerodynamic load loading method used for reliability tests on aircraft flap and slat system
An aerodynamic load and reliability technology, applied in aerodynamic tests, machine/structural component testing, measuring devices, etc., can solve problems such as unrealistic environmental conditions, high cost, and complexity of large and complex mechanical products, and achieve easy Control and realization, the effect of uniform force
- Summary
- Abstract
- Description
- Claims
- Application Information
AI Technical Summary
Problems solved by technology
Method used
Image
Examples
Embodiment Construction
[0053] The above and other technical features and advantages of the present invention will be described in more detail below in conjunction with the accompanying drawings.
[0054] see figure 1 Shown, it is the flowchart of the aerodynamic load loading method of reliability test of the present invention, and this specific process is:
[0055] Step a, obtain the aerodynamic load of the slat in each flight state through wind tunnel test or simulation calculation;
[0056] Step b, according to the aerodynamic loads of the aircraft slats in different flight states, calculate the resultant force of the aerodynamic loads on the slat surface in each flight state;
[0057]Step c, according to the resultant force of the aerodynamic load on the slat wing surface of the aircraft in each flight state, decompose it into several component forces, and obtain the magnitude and direction of the component forces;
[0058] Step d, uniformly distribute and load the component force of the above ...
PUM
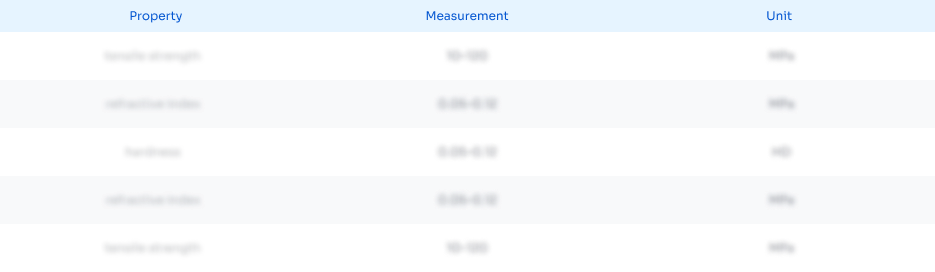
Abstract
Description
Claims
Application Information

- Generate Ideas
- Intellectual Property
- Life Sciences
- Materials
- Tech Scout
- Unparalleled Data Quality
- Higher Quality Content
- 60% Fewer Hallucinations
Browse by: Latest US Patents, China's latest patents, Technical Efficacy Thesaurus, Application Domain, Technology Topic, Popular Technical Reports.
© 2025 PatSnap. All rights reserved.Legal|Privacy policy|Modern Slavery Act Transparency Statement|Sitemap|About US| Contact US: help@patsnap.com