Solder-wire-free high-frequency automatic welding method for storage battery connecting piece
An automatic welding and storage battery technology, which is applied in the direction of high-frequency current welding equipment, welding equipment, battery assembly machines, etc., can solve the problems of relatively large fluctuations in welding quality, physical injury of welding workers, and difficulty in ensuring welding quality, so as to save manpower Material resources, welding time shortening, and the effect of ensuring welding quality
- Summary
- Abstract
- Description
- Claims
- Application Information
AI Technical Summary
Problems solved by technology
Method used
Image
Examples
Embodiment Construction
[0025] Embodiment of the present invention: a high-frequency automatic welding method for battery connecting pieces without welding wire, as shown in the attached Figure 1-5 As shown, the main process of this welding method is to insert the connecting piece 6 onto the battery terminal 5 exposed from the head end of the battery, and then send the battery to the high-frequency automatic welding machine through the conveying mechanism 1 of the high-frequency automatic welding machine After sending to the flux adding station, the flux adding mechanism 2 will spray flux on the head end of the battery terminal 5 and the connecting piece 6. After the flux application is completed, the workpiece moving mechanism 3 will move the battery to the worker to be welded. position, then the welding mechanism 4 goes down so that the welding coil 43 of the welding mechanism is located above the head end of the battery terminal 5, and the high-frequency power generator 42 of the welding mechanism...
PUM
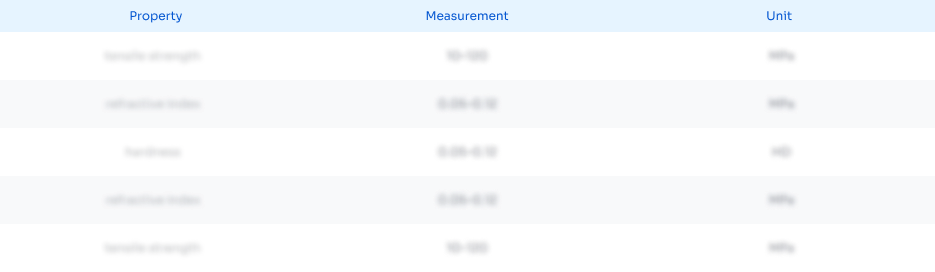
Abstract
Description
Claims
Application Information

- Generate Ideas
- Intellectual Property
- Life Sciences
- Materials
- Tech Scout
- Unparalleled Data Quality
- Higher Quality Content
- 60% Fewer Hallucinations
Browse by: Latest US Patents, China's latest patents, Technical Efficacy Thesaurus, Application Domain, Technology Topic, Popular Technical Reports.
© 2025 PatSnap. All rights reserved.Legal|Privacy policy|Modern Slavery Act Transparency Statement|Sitemap|About US| Contact US: help@patsnap.com