Preparation method of nanocrystalline metal catalyst loaded with carbon and nitrogen materials
A technology of nano-metal and carbon-nitrogen materials, applied in chemical instruments and methods, physical/chemical process catalysts, amino compound preparation, etc., can solve the problems of increasing reaction conditions, agglomeration deactivation, low activity, etc., and achieve high catalytic performance, Not easy to reunite and not easy to deactivate
- Summary
- Abstract
- Description
- Claims
- Application Information
AI Technical Summary
Problems solved by technology
Method used
Image
Examples
Embodiment example 1
[0013] Weigh 0.11g of ruthenium (III) chloride hydrate (ruthenium content 37%) in a round bottom flask, 20mL of acetone as solvent, and then add 0.21g of ligand L1 (the molar ratio of metal ruthenium to ligand is 1:2.89) , After stirring at 30° C. for 3 h, 2 g of activated carbon was slowly added. The round bottom flask was heated in an oil bath at 50°C, and after stirring at 50°C for 6h, the solvent acetone was removed by rotary evaporation. The obtained supported pre-catalyst was vacuum-dried at 50° C. for 12 hours. The dried pre-catalyst was placed in a tube furnace and calcined at 800° C. for 2 h under nitrogen (heating rate 4° C. / min). After naturally falling to a constant temperature, a catalyst C1 (with a ruthenium loading of 2%) was obtained.
Embodiment example 2
[0015] Weigh 0.09g rhodium dipolyacetate (rhodium content 46.5%) in a round bottom flask, 20mL ethanol as solvent, then add 0.21g ligand L1 (the molar ratio of metal rhodium to ligand is 1:2.86), and stir at 30°C After 3 h, 2 g of activated carbon was slowly added. The round bottom flask was heated in an oil bath at 60°C, stirred at 50°C for 6h, and then the solvent ethanol was removed by rotary evaporation. The obtained supported pre-catalyst was vacuum-dried at 50° C. for 10 h. The dried pre-catalyst was placed in a tube furnace and calcined at 800°C for 2h under nitrogen (heating rate 4°C / min). After naturally lowering to a constant temperature, catalyst C2 (with rhodium loading of 2.1%) was obtained.
Embodiment example 3
[0017] Weigh 0.08g iridium(III) chloride hydrate (iridium content 52%) in a round bottom flask, 20mL ethanol is used as a solvent, after ultrasonication at room temperature for 3h, add 0.11g ligand L1 (metal iridium and ligand The molar ratio is 1:2.82), then continue stirring at 25°C for 2h, and slowly add 2g of activated carbon. The round bottom flask was heated in an oil bath at 40°C, stirred at 50°C for 5h, and the solvent ethanol was removed by rotary evaporation. The obtained supported pre-catalyst was vacuum-dried at 60° C. for 11 h. The dried pre-catalyst was placed in a tube furnace and calcined at 800°C for 2h under nitrogen (heating rate 4°C / min). After naturally falling to a constant temperature, catalyst C3 (2.1% iridium loading) was obtained.
PUM
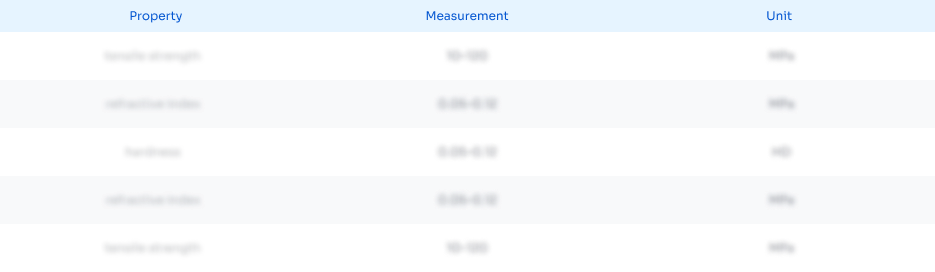
Abstract
Description
Claims
Application Information

- R&D
- Intellectual Property
- Life Sciences
- Materials
- Tech Scout
- Unparalleled Data Quality
- Higher Quality Content
- 60% Fewer Hallucinations
Browse by: Latest US Patents, China's latest patents, Technical Efficacy Thesaurus, Application Domain, Technology Topic, Popular Technical Reports.
© 2025 PatSnap. All rights reserved.Legal|Privacy policy|Modern Slavery Act Transparency Statement|Sitemap|About US| Contact US: help@patsnap.com