Vegetable fiber inorganic lightweight filling aggregates
A plant fiber and inorganic technology, applied in the field of building materials, can solve the problems of easy moth, perishability, porous water absorption, etc., and achieve the effect of overcoming perishability, improving hardness, and improving waterproof performance.
- Summary
- Abstract
- Description
- Claims
- Application Information
AI Technical Summary
Problems solved by technology
Method used
Image
Examples
Embodiment 1
[0025] Add 4 / 5 tank capacity of magnesium chloride solution with a concentration of 20% and a temperature of 25 degrees Celsius in the mixing tank of the cement mortar mixer, then add 2 / 3 tank capacity of plant fiber and stir for 5 minutes to degrease, then add the weight of plant fiber 45% of the amount of fly ash with a mesh number of 300 mesh was stirred for 5 minutes to fill the holes, and then an aqueous sodium methyl silicate solution with a weight of 1:20 accounting for 30% of the amount of the fly ash was added and stirred for 5 minutes to gel; After the gelling treatment, the plant fibers are taken out and drenched to make the water content 35%, and then put into the air-flow dryer for drying, so that the water content is 5%, and then made into particles with a fineness of 80 meshes to form the Inorganic light-weight filler aggregates of plant fibers are put into inner membrane waterproof bags for later use.
Embodiment 2
[0027] In the mixing tank of the cement mortar mixer, add 4 / 5 tank capacity of magnesium chloride solution with a concentration of 20% and a temperature of 28 degrees Celsius, add 2 / 3 tank capacity of plant fiber and stir for 5 minutes to degrease, then add the weight accounted for the amount of plant fiber. 47%, the mesh number is 330 mesh fly ash and stirs for 5 minutes to fill the holes, then add 1:20 weight accounted for 33% sodium methyl silicate aqueous solution of the amount of the fly ash and stir for 5 minutes to gel; After the gelling treatment, the plant fibers are drenched to make the water content 35%, and then put into the airflow dryer for drying, so that the water content is 7%, and then made into 90 mesh fineness particles to form plant fiber inorganic light Quality filling aggregate, put into inner membrane waterproof bag for subsequent use, the stirring time of each step is identical with embodiment 1.
Embodiment 3
[0029] In the mixing tank of the cement mortar mixer, add 4 / 5 tank capacity of magnesium chloride solution with a concentration of 20% and a temperature of 29 degrees Celsius, add 2 / 3 tank capacity of plant fiber and stir for 5 minutes to degrease, then add the weight accounted for the amount of plant fiber. 50% fly ash with a mesh number of 350 was stirred for 5 minutes to fill the holes, then added a 1:20 aqueous solution of sodium methyl silicate that accounted for 35% of the amount of the fly ash and stirred for 5 minutes to gel; After the gelling treatment, the plant fibers are drenched to make the water content 35%, and then put into the airflow dryer for drying, so that the water content is 8%, and then made into particles with a fineness of 100 meshes to form the plant fiber inorganic The lightweight filling aggregate is put into an inner film waterproof bag for subsequent use, and the stirring time of each step is the same as that of Example 1.
PUM
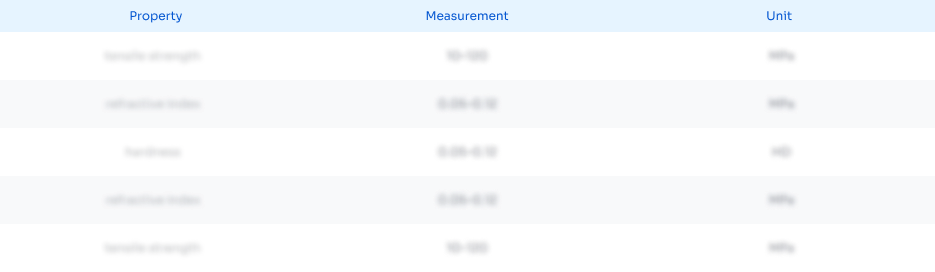
Abstract
Description
Claims
Application Information

- R&D
- Intellectual Property
- Life Sciences
- Materials
- Tech Scout
- Unparalleled Data Quality
- Higher Quality Content
- 60% Fewer Hallucinations
Browse by: Latest US Patents, China's latest patents, Technical Efficacy Thesaurus, Application Domain, Technology Topic, Popular Technical Reports.
© 2025 PatSnap. All rights reserved.Legal|Privacy policy|Modern Slavery Act Transparency Statement|Sitemap|About US| Contact US: help@patsnap.com