Production process for three-dimensional art glass
A technology of art glass and production technology, which is applied in glass molding, glass reshaping, glass manufacturing equipment, etc., can solve the problems of poor ink glaze adhesion, difficulty in obtaining glazed art glass, and easy damage, etc., to achieve Improve adhesion and integrity, good three-dimensional molding effect, and improve structural stability
- Summary
- Abstract
- Description
- Claims
- Application Information
AI Technical Summary
Problems solved by technology
Method used
Examples
Embodiment 1
[0024] Example 1: The production process of single-sided solid-color three-dimensional art glass
[0025] Take the float glass, cut the material, and then polish and clean the edge to obtain the glass substrate.
[0026] Take the glass substrate, screen or roller print the first layer of solid color ink on the first surface, and the ink coating amount is 180-200g / m 2 , drying at 150-200°C for 300-400 seconds and cooling to room temperature. Then screen or roller print the second layer of protective ink on the first surface of the glass substrate, and the ink coating amount is 180-200g / m 2 , drying at 150-200°C for 300-400 seconds and cooling to room temperature. Subsequently, the glass substrate is sintered at a constant temperature of 690-720°C for 360-400 seconds, and then cooled by air quenching for 100-200 seconds to lower the temperature of the glass substrate to below 100°C to obtain a semi-finished glass.
[0027] Take a three-dimensional mold with a concave-convex t...
Embodiment 2
[0028] Embodiment 2: Production process of three-dimensional art glass with single-sided pattern
[0029] Take the float glass, cut the material, and then polish and clean the edge to obtain the glass substrate.
[0030] Take the glass substrate, print the first layer of pattern ink on the first surface with screen or roller, dry at 150-200°C for 300-400 seconds and cool to room temperature, then print the second layer with screen or roller solid-color ink, then dry at 150-200°C for 300-400 seconds and cool to room temperature, the coating amount of pattern ink and solid-color ink is 180-200g / m 2 . Then, screen or roller print the third layer of protective ink on the first surface of the glass substrate, and the ink coating amount is 180-200g / m 2 , drying at 150-200°C for 300-400 seconds and cooling to room temperature. Subsequently, the glass substrate is sintered at a constant temperature of 690-720°C for 360-400 seconds, and then cooled by air quenching for 100-200 secon...
Embodiment 3
[0032] Embodiment 3: Production process of double-sided pure color three-dimensional art glass
[0033] Take the float glass, cut the material, and then polish and clean the edge to obtain the glass substrate.
[0034] Take the glass substrate, screen or roller print the first layer of solid color ink on the first surface, and the ink coating amount is 180-200g / m 2 , drying at 150-200°C for 300-400 seconds and cooling to room temperature. Then screen or roller print the second layer of protective ink on the first surface of the glass substrate, and the ink coating amount is 180-200g / m 2 , drying at 150-200°C for 300-400 seconds and cooling to room temperature. Subsequently, the glass substrate is sintered at a constant temperature of 690-720° C. for 360-400 seconds, and then cooled by air quenching for 100-200 seconds to lower the temperature of the glass substrate to below 100° C. Then, screen or roller print a layer of solid color ink on the second surface of the glass su...
PUM
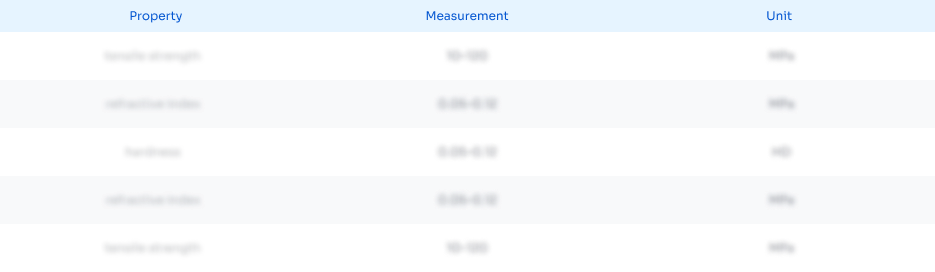
Abstract
Description
Claims
Application Information

- R&D
- Intellectual Property
- Life Sciences
- Materials
- Tech Scout
- Unparalleled Data Quality
- Higher Quality Content
- 60% Fewer Hallucinations
Browse by: Latest US Patents, China's latest patents, Technical Efficacy Thesaurus, Application Domain, Technology Topic, Popular Technical Reports.
© 2025 PatSnap. All rights reserved.Legal|Privacy policy|Modern Slavery Act Transparency Statement|Sitemap|About US| Contact US: help@patsnap.com