Permanent magnet motor and compressor
A permanent magnet motor and motor technology, applied in the field of compressors and permanent magnet motors, can solve the problems of increasing motor stop frequency, reducing system reliability, increasing current, etc., to suppress current increase, improve reliability, and suppress overcurrent detection. Effect
- Summary
- Abstract
- Description
- Claims
- Application Information
AI Technical Summary
Problems solved by technology
Method used
Image
Examples
Embodiment 1
[0026] figure 1 It is a cross-sectional structural diagram of a compressor according to an embodiment of the present invention. exist figure 1 Among them, the compression mechanism portion is formed by engaging the spiral wrap 15 standing upright on the end plate 14 of the fixed scroll member 13 and the spiral wrap 18 standing upright on the end plate 17 of the orbiting scroll member 16 . By orbiting the orbiting scroll member 16 by the crankshaft 6 , the air sucked in from the suction pipe 23 is compressed.
[0027] Among the compression chambers 19 (19a, 19b, . . . ) formed by the fixed scroll member 13 and the orbiting scroll member 16, the compression chamber 19 located on the outermost radial side moves toward the two scroll members 13 with the orbiting motion. , The center of 16 moves, and the volume gradually shrinks. When the two compression chambers 19a and 19b reach the vicinity of the centers of the fixed scroll member 13 and the orbiting scroll member 16 , the...
Embodiment 2
[0040] Below, use image 3 Instead, Embodiment 2 of the present invention will be described.
[0041] The structure described in Example 1 can output torque suitable for the fluctuation of the load, but on the other hand, since the protruding part is provided in the direction of the gap, the stator may be distorted due to shaft deviation and eccentricity during motor assembly. The inner diameter mechanically interferes with the rotor outer diameter. When interference occurs, vibration and noise may increase. In order to avoid mechanical interference, increase in vibration and noise, if the gap length when the protruding parts face each other is adapted to the level of the conventional design, the gap length of the non-protruding part becomes too large, and it cannot be generated during periods other than the peak of the pulsation. sufficient torque.
[0042] A method for solving this problem will be described in this embodiment. That is, the permanent magnet motor of the p...
Embodiment 3
[0050] Below, use Figure 4 ~ Figure 6 Embodiment 3 of the present invention will be described.
[0051] Figure 4 It is a radial sectional view showing the permanent magnet motor of this embodiment. exist Figure 4 in, with figure 2 The same reference numerals are attached to the same constituent elements to avoid repeated explanations. Figure 4 structure with figure 2 The difference is that a stator slit 53 (cavity) is first provided on at least one stator tooth 52 of the stator teeth 52, and a position where magnetic flux transmission becomes easy (stator magnetic flux transmission facilitation portion 56) is relatively provided. On the other hand, among the plurality of poles of the rotor 1, the rotor slit 7 (cavity) is provided in a part of the magnetic body constituting the pole, and by connecting at least one pole of the rotor 1 with the Compared with the plurality of poles of the rotor slit 7, the cross-sectional area of the slit is reduced or the slit is el...
PUM
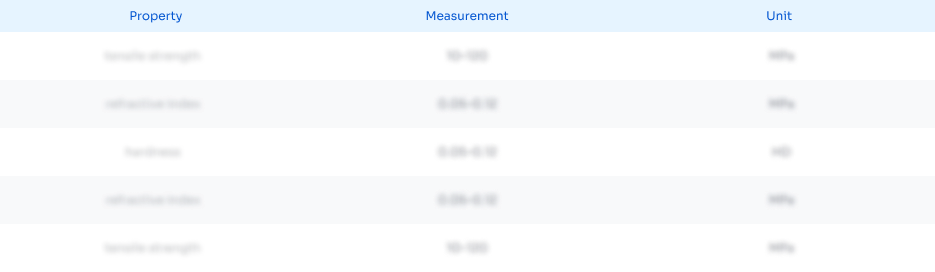
Abstract
Description
Claims
Application Information

- R&D
- Intellectual Property
- Life Sciences
- Materials
- Tech Scout
- Unparalleled Data Quality
- Higher Quality Content
- 60% Fewer Hallucinations
Browse by: Latest US Patents, China's latest patents, Technical Efficacy Thesaurus, Application Domain, Technology Topic, Popular Technical Reports.
© 2025 PatSnap. All rights reserved.Legal|Privacy policy|Modern Slavery Act Transparency Statement|Sitemap|About US| Contact US: help@patsnap.com