Mining wind-leaking-stoppage phenol-urea-formaldehyde foam resin, composite foam and preparation method of composite foam
A foamed resin and composite foam technology, used in mining equipment, earth-moving drilling, filling, etc., can solve the problems of high temperature divergence, weak pressure bearing capacity, low production cost, etc., and achieve flame retardancy and thermal stability. Good properties, high elasticity and compressive strength, high foaming ratio
- Summary
- Abstract
- Description
- Claims
- Application Information
AI Technical Summary
Problems solved by technology
Method used
Image
Examples
Embodiment Construction
[0016] In order to make the purpose, technical solutions and advantages of the present invention clearer, the technical solutions in the present invention will be clearly and completely described below. Apparently, the described embodiments are some embodiments of the present invention, rather than all embodiments. Based on the embodiments of the present invention, all other embodiments obtained by persons of ordinary skill in the art without making creative efforts belong to the protection scope of the present invention.
[0017] The following first introduces the raw material composition and preparation process of phenol urea-formaldehyde foaming resin.
[0018] The present invention takes phenol, urea element and paraformaldehyde as raw materials, synthesizes phenol urea-formaldehyde foaming resin by controlling conditions such as reaction time, temperature, analyzes reaction temperature, time, material proportion, catalyst consumption and other factors to the viscosity of f...
PUM
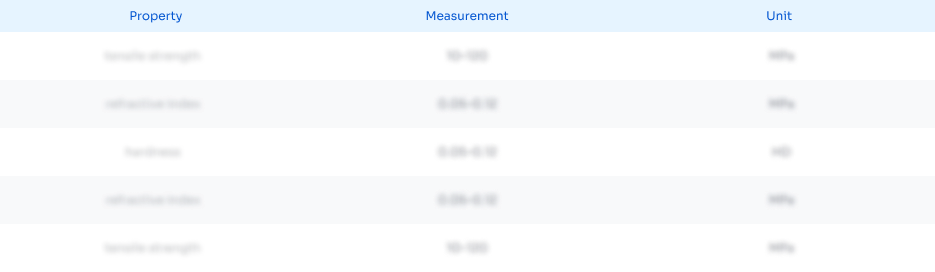
Abstract
Description
Claims
Application Information

- Generate Ideas
- Intellectual Property
- Life Sciences
- Materials
- Tech Scout
- Unparalleled Data Quality
- Higher Quality Content
- 60% Fewer Hallucinations
Browse by: Latest US Patents, China's latest patents, Technical Efficacy Thesaurus, Application Domain, Technology Topic, Popular Technical Reports.
© 2025 PatSnap. All rights reserved.Legal|Privacy policy|Modern Slavery Act Transparency Statement|Sitemap|About US| Contact US: help@patsnap.com