Oriented vibrating wheel system of driving gear box structure of road roller
A technology of gear box structure and vibrating wheel, which is applied in the field of road roller equipment, can solve problems such as shortening the service life of gears, uncoordinated vibration between teeth, and affecting meshing coordination, so as to reduce impact collision force and friction force, and compensate for coaxiality The effects of small errors and increased service life
- Summary
- Abstract
- Description
- Claims
- Application Information
AI Technical Summary
Problems solved by technology
Method used
Image
Examples
Embodiment Construction
[0029] For ease of understanding, the attached Figure 1-3 Concrete structure and workflow of the present invention are described as follows:
[0030] Concrete structure of the present invention, can refer to figure 1As shown, it specifically includes a vibrating wheel 10 as an external steel wheel. The vibrating wheel has a built-in cylinder 70. The rotating shaft 20 is supported and fixed with a bearing in the cylindrical body 70. An external power source 40 (that is, a vibrating motor) is arranged on one side of the rotating shaft 20. ). The rotating shaft 20 is arranged in sequence from the end where the external power source 40 is located to the other end of the first forward rotation eccentric block group 61, the direction changing gear set 50, the reverse rotation eccentric block group 30 and the second forward rotation eccentric block group 62; A positive rotation eccentric block group 61 and a reverse rotation eccentric block group 30 are both sleeved on the rotatin...
PUM
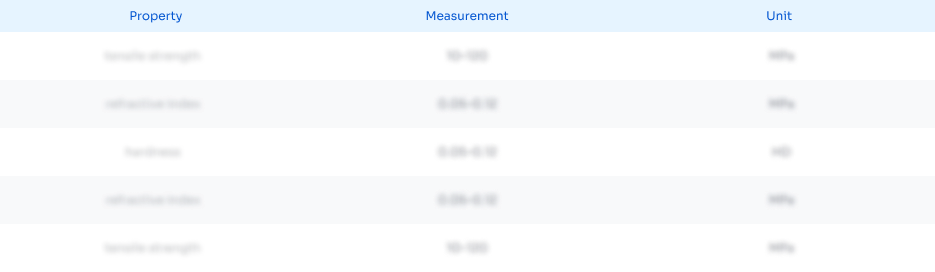
Abstract
Description
Claims
Application Information

- R&D
- Intellectual Property
- Life Sciences
- Materials
- Tech Scout
- Unparalleled Data Quality
- Higher Quality Content
- 60% Fewer Hallucinations
Browse by: Latest US Patents, China's latest patents, Technical Efficacy Thesaurus, Application Domain, Technology Topic, Popular Technical Reports.
© 2025 PatSnap. All rights reserved.Legal|Privacy policy|Modern Slavery Act Transparency Statement|Sitemap|About US| Contact US: help@patsnap.com