Method and device for producing a composite sheet-metal part with a metal edge region
A technology of edge area and manufacturing method, applied in the direction of manufacturing tools, metal processing equipment, welding of straight welds, etc., can solve the problems of time-consuming, difficult to realize automation, etc., and achieve the effect of comprehensive exclusion
- Summary
- Abstract
- Description
- Claims
- Application Information
AI Technical Summary
Problems solved by technology
Method used
Image
Examples
Embodiment Construction
[0040] First, in figure 1 A first embodiment of the method according to the invention is shown in , in which the composite panel part 1 consists of two outer cover panels 2, 3 and a plastic layer 4 arranged between the cover panels 2, 3 The composite panel part is heated in its edge region 5 in such a way that the plastic layer 4 in this edge region 5 softens. Heating of the edge region 5 can take place in different ways and in different ways. In the present exemplary embodiment, the current is introduced into the composite panel part 1 via the rollers 6 and the conductive clips 7 and via the bracket 8, wherein in particular in the contact region of the rollers 6, that is to say in the edge region 5 for the upper and Optionally, the lower cover plates 2 , 3 are heated so intensely that the plastic layer 4 arranged in the edge region 5 becomes considerably softer. Due to the force transferred to the rollers 6 in the direction of the composite panel part 1 , the upper cover 2 ...
PUM
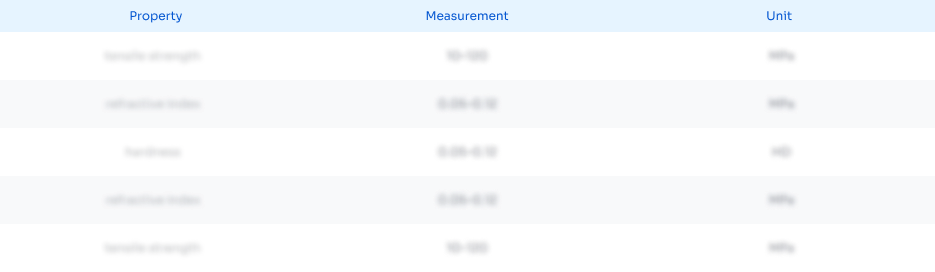
Abstract
Description
Claims
Application Information

- R&D
- Intellectual Property
- Life Sciences
- Materials
- Tech Scout
- Unparalleled Data Quality
- Higher Quality Content
- 60% Fewer Hallucinations
Browse by: Latest US Patents, China's latest patents, Technical Efficacy Thesaurus, Application Domain, Technology Topic, Popular Technical Reports.
© 2025 PatSnap. All rights reserved.Legal|Privacy policy|Modern Slavery Act Transparency Statement|Sitemap|About US| Contact US: help@patsnap.com