Fabrication method of circular PPTC thermistor
A thermistor and ring-shaped technology, which is applied in the field of preparation of ring-shaped PPTC thermistors, can solve the problems of uneven heating, uneven arrangement thickness, and uneven irradiation in heat treatment, so as to improve heat treatment efficiency and save Irradiation cost, good effect of resistance consistency
- Summary
- Abstract
- Description
- Claims
- Application Information
AI Technical Summary
Problems solved by technology
Method used
Image
Examples
Embodiment 1
[0043] In this embodiment, the substrate components are 4000 g of high-density polyethylene, 4300 g of carbon black, and 1000 g of magnesium hydroxide.
[0044] Concrete method steps among the present embodiment are:
[0045] 1) Substrate treatment: Substrate batching, crushing, and mixing The substrate batching is carried out according to the above components, and then the substrate is poured into a mixer and mixed evenly.
[0046] 2) Twin-screw extruder extrusion and calendering: After mixing in step 1), the base material is vacuum-extruded and calendered by a twin-screw extruder to form a PTC plate with a thickness of 0.28 to 0.32 mm; the extrusion temperature of the twin-screw extruder is 190~200℃.
[0047] 3) After the formed plate is cooled, it is punched, and punched and cut into Φ16.3*Φ10.0 (outer circle*inner circle, unit mm) chips by punching die. Such as figure 1 As shown, a plurality of string rods 1 are arranged below the die hole of the punch die, and the ring...
Embodiment 2
[0057] As a further improvement of the present invention, in step 3), such as figure 1 As shown, a lifting plate 4 is connected to the bottom of the string rod 1 , and a jacking device 5 is arranged below the lifting plate 4 . When the lifting plate 4 rises, the skewer 1 is inserted into the mold hole. When the product is in place, the photoelectric sensor stops the punching machine, the lifting plate 4 is lowered, and a new stringer 1 is replaced. The operation is simple and convenient.
[0058] When the string rods with ring-shaped PPTC thermistors are turned over and transported, storage tools with handles on both sides are used. The distance between each layer of products is greater than 1mm, and it can be taken out in a single layer.
[0059] The preparation method of the present invention is suitable for preparing circular PPTC thermistors made of the following various raw materials. The circular PPTC thermistors include a base material and nickel-plated copper foils com...
PUM
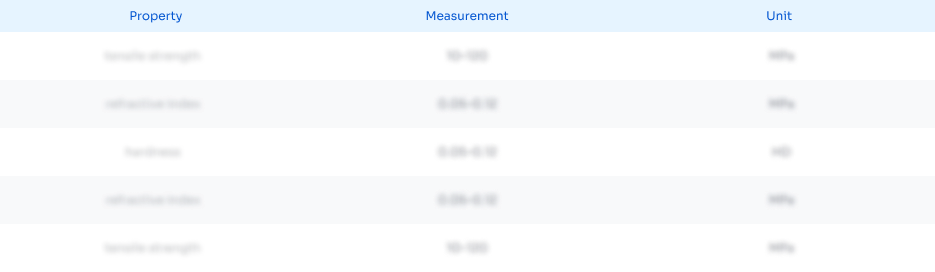
Abstract
Description
Claims
Application Information

- Generate Ideas
- Intellectual Property
- Life Sciences
- Materials
- Tech Scout
- Unparalleled Data Quality
- Higher Quality Content
- 60% Fewer Hallucinations
Browse by: Latest US Patents, China's latest patents, Technical Efficacy Thesaurus, Application Domain, Technology Topic, Popular Technical Reports.
© 2025 PatSnap. All rights reserved.Legal|Privacy policy|Modern Slavery Act Transparency Statement|Sitemap|About US| Contact US: help@patsnap.com