Wide-range fiber bragg grating displacement sensor and measuring method
A technology of displacement sensor and optical fiber grating, applied in the field of displacement sensor, can solve the problems of poor anti-interference ability in the field environment, difficulty in long-distance signal transmission, lagging of real-time monitoring system, etc., achieve unique application value, reduce types and quantities, and simple structure Effect
- Summary
- Abstract
- Description
- Claims
- Application Information
AI Technical Summary
Problems solved by technology
Method used
Image
Examples
Embodiment Construction
[0036] Below in conjunction with accompanying drawing and embodiment the present invention will be further described:
[0037] Such as figure 1 and Figure 7 As shown, a large-range fiber grating displacement sensor includes a main body of the sensor and a wire rope fixing structure. The main body of the sensor is composed of a shell and an internal structure.
[0038] The shell part is composed of lower cover 16, optical cable fixing joint 17, armored optical cable 18, cylinder side wall 19, upper cover 20; the internal structure part is composed of optical fiber 1, strain beam 2, fiber grating 1, fiber grating 2 4, precision Screw rod 5, support one 6, reel 7, steel wire rope 8, fixed nut 9, spring box 10, support two 11, scroll spring 12, set screw one 13, locking screw 14, set screw two 15 form.
[0039] The wire rope structure includes 21 wire rope buckles and 22 wire rope fixing rings.
[0040] The optical fiber 1 is one, and the optical fiber 1 is strung with a fiber...
PUM
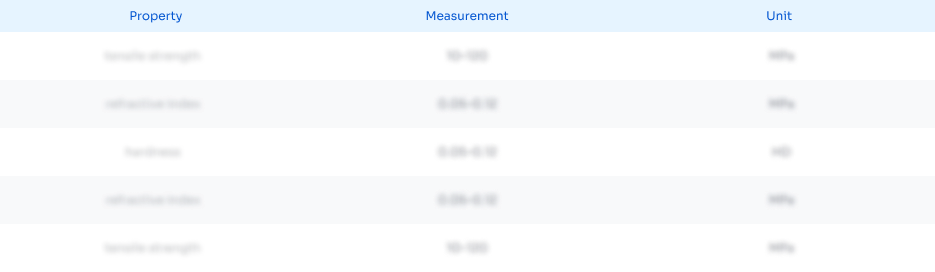
Abstract
Description
Claims
Application Information

- R&D Engineer
- R&D Manager
- IP Professional
- Industry Leading Data Capabilities
- Powerful AI technology
- Patent DNA Extraction
Browse by: Latest US Patents, China's latest patents, Technical Efficacy Thesaurus, Application Domain, Technology Topic, Popular Technical Reports.
© 2024 PatSnap. All rights reserved.Legal|Privacy policy|Modern Slavery Act Transparency Statement|Sitemap|About US| Contact US: help@patsnap.com