LFT-D molding process for glass fiber reinforced PA
A technology of LFT-D and glass fiber, which is applied in the field of LFT-D molding technology, can solve the problems of difficulty in achieving uniform dispersion of long fibers, weakening of glass fiber reinforcement effect, unfavorable fiber full infiltration, etc., to achieve short molding cycle, easy curing, Energy Saving Effect
- Summary
- Abstract
- Description
- Claims
- Application Information
AI Technical Summary
Problems solved by technology
Method used
Image
Examples
Embodiment Construction
[0018] Such as figure 1 Shown, the LFT-D molding process of glass fiber reinforced PA of the present invention comprises:
[0019] Step 10. Add PA to the first-stage twin-screw extruder for melt plasticization. The PA is PA6 or PA66. The speed of the first-stage twin-screw extruder is set to 130-270rpm / min, and the temperature of the extruder is set to The temperature is 240~280℃; the molten PA material passes through the die of the first-stage twin-screw extruder to form a polymer film;
[0020] Step 20, cutting the glass fiber into pieces; each section is about 24-25mm long;
[0021] Step 30, combining the cut glass fibers with the polymer film and dispersing them into the polymer film, wherein the amount of PA is 50-70% of the total mass, and the amount of glass fiber is 30-50% of the total mass;
[0022] Step 40, after the glass fiber and the polymer film are merged, enter the second-stage twin-screw extruder together, and the glass fiber and PA are fully mixed under the...
PUM
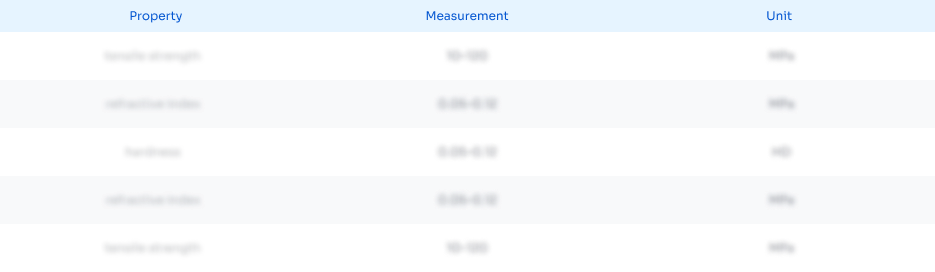
Abstract
Description
Claims
Application Information

- R&D Engineer
- R&D Manager
- IP Professional
- Industry Leading Data Capabilities
- Powerful AI technology
- Patent DNA Extraction
Browse by: Latest US Patents, China's latest patents, Technical Efficacy Thesaurus, Application Domain, Technology Topic, Popular Technical Reports.
© 2024 PatSnap. All rights reserved.Legal|Privacy policy|Modern Slavery Act Transparency Statement|Sitemap|About US| Contact US: help@patsnap.com